What is a CNC Knife Cutting Machine?
How Does a CNC Knife Cutting Machine Work?
The cutting process with high precision accuracy has been automated with the computer numerical control (CNC) technology of these CNC knife cutting machines. The machine uses a blade to cut across the material by interpreting a digital design file which guides the machine on the cutting paths. The software takes control of the cutting tool’s motion and can, therefore, execute elaborate designs and forms of any shape without human control. This advancement not only enhances the level of output reliability but also decreases the amount of manual work and the level of mistakes.
If you are looking for more information about Top CNC Knife Cutting Machine Provider in China – Dekcel go here right away.
What materials can be cut with a CNC Knife cutter?
Due to the wide range of materials that can be processed by the CNC knife cutting machines, they are quite flexible. Some of the most common of these are foam, textiles, rubber, leather, paper, cardboard, composites and PVC. These machines are also capable of cutting soft and semi rigid materials for packaging, automotive, garments and sign making industries. Since there are many construction materials that the CNC knife cutter can work with, it is an important tool in a number of industries.
For more in-depth information you should view from CNC Knife Cutting Machine – Dekcel
Perks of Operating a CNC Cutting Machine
Cost effectiveness is certainly one of the most important benefits of employing a CNC knife cutting machine and in addition to this precision also and efficiency cut waste on material. There is also less dependence on manual labor for the processes making the time of production shorter. With respect to mass production, all cuts are very consistent in terms of quality; also, changes to the designs can be made through the machine’s software, which provides great ease in the creation of prototypes.
How to Choose the Right Digital Cutting Machine?
What to Consider When Selecting a CNC Router Machine
- Materiality: Outline the types of materials envisaged for use with the CNC router so as to make sure that the machine can cope with the wood, metals and plastics cutting requirements.
- Dimensions of the Work Zone: Identify how extended the work area is required to be. This is to say that the machine must be capable of adapting to the biggest projects that can be anticipated but at the same time be able to operate efficiently.
- Rotor Performance: Evaluate the power rating and / or the power up and speed rating of the spindle. A high rotational speed is sufficient to cut softer materials but is quite inadequate for cutting tougher materials.
- Operability and Compatibility: Examine the usability and integration with existing design packages. If the software is easy to operate, the processes will be more effective, and less time will be required for the operator to be trained.
- Cost Factors: Ensure that the features required are within the budget considering both the bare price and ongoing maintenance and periodic repairs.
Are Oscillating Knife Cutting Machines Suitable for All Materials?
Oscillating knife cutting machines are able to perform great versatility although they may not be appropriate for all the materials. For low to medium rigid materials such as leather, foam as well as textiles they are excellent but they may have some restrictions on very hard or thick materials such as metals and some plastics. The choice of an oscillating knife cutter should be coupled with the type of materials and requirements of the application.
How to Evaluate Cutting Tools for CNC Digital Knife Cutting
- Tooling Compatibility: Ensure that the cutting tools being employed are of the appropriate type for the materials being processed so as to enhance cutting efficiency and the life span of the tools used.
- Toughness and Abrasion Resistance: Take note of how tough the tool is and its resistance to abrasion under long heightened usage.
- Cutting Accuracy: To comprehend the level of cutting accuracy guaranteed by the tool, considering that accurate cutting of workpieces is paramount in the quality of the product.
- Timeliness and Productivity: Always pay attention to the cutting speed of the tool and it’s relevance on cycle time for production.
- Cost-benefit: Understand the initial outlay of a tool in relation to the anticipated benefits in terms of productivity and cut size minimization.
Top Applications for CNC Knife Cutting
Industries Benefiting from CNC Knife Cutting Machines
- Textile and Apparel: These garments cutting machines are accurate, efficient and cost effective as they help to minimize wastage of materials and maximize output. They allow for accurate cutting of fabrics for clothing, upholstery and other forms of textiles.
- Packaging: The packaging die cut designs have better accuracy and can be used in both custom and mass production industries.
- Automotive: These cutting sieves play a pivotal role as they assist in the processes of forming and making the various interior parts like leather or fabric seat covers which require a lot of consistency and quality.
- Signage and Graphics: These CNC knife cutting machines increase speed and efficiency of the cutting by allowing cutting of other materials apart from vinyl which are used in crafting signs and graphics plus display solutions.
- Footwear: These cutting spares are essential in cuttng synthetic and leather materials which are used in the shoe making process while enabling the patterns to be cut precisely and accurately.
How Digital Knife Cutting is Used in Fabric Cutting
Digital knife cutting is within fabric applications meaning it is possible to repeat patterns in a fabric without slitting or distortions. Such technology allows for intricate patterns and designs with low on the raw materials and labour human input. It is multi faceted hence applicable on mock up, small quantities as well as large quantity production.
CNC Foam Cutting Machines With Oscillating Blade
Foam can be cut using CNC machines with oscillating blades. They can be utilized to create packaging inserts, foam models, gaskets, and so on because they can create clean cuts without compression or distortion. Also, the cutting action enables them to efficiently and accurately cut more robust and thicker types of foam.
Maintenance Tips for Your CNC Cutting Machine
How to Maintain a Digital Cutter for Optimal Performance
Every digital cutter needs regular cleaning and inspection for optimum service regardless of whether it’s the first use or the one-hundredth use of the cutter. Furthermore, a clean cutting table is extremely important because if left without proper cleaning, debris will build up and it will impact the cutting capabilities. Regularly inspecting the blade, tool, and spindle conditions is necessary because these parts determine how well the cut is made as neglecting them can have a negative outcome. There are parts that move and if they move too closely to each other or rub against each other it will lead to wear and tear; lubrication can prevent that according to a manufacturer’s instructions. In order for the equipment to be efficient and effective at its job, regular software updates and calibrations need to be made.
What are some solutions for the problems with CNC Knife Cutting Machines?
Some problems with CNC knife cutting machines involve the tearing of the blade, the spindle not being in the center, or the installed software crashing. Several cutting tasks especially with blades start to wear out especially when cutting tough or abrasive materials as this leads to imprecise cuts. Often times cutting the same width in the same direction repetitively results in deformation through mechanical displacement causing the workpiece to come out misaligned, and as a result only part of the workpiece is cut through. Lack of maintaining the software or forcing an underground program to run can cause issues with any equipment as it makes the control functions ineffective. These issues are more often than not resolved as they are quite self-explanatory and are part of regular maintenance.
How to Extend the Cutting Tools Life in CNC Machines
An operator’s first concern when it comes to CNCmachines is cutting tools. Cnc machines utilize a myriad tools and blades, from end Mills to lathes and specialized attachments. A zillion cutting blades can be damaged or even destroyed, so the machine can not function properly. To ease this concern it is important to utilize quality cutting blades. Further adding that the blades are optimal for the specific material that is to be worked on. Additionally avoid the overuse of specific tools by alternating its use with others. Another factor that comes to consider was the settings used for the cutting. Having appropriate settings will not only reduce the operators stress but also wear and tear. Furthermore, routine maintenance and cleaning should be done on the machine along with its tool holding mechanisms. This action will prevent unnecessary damage to the cutting tools and yield a successful cutting operation.
Cost and ROI of CNC Knife Cutting Machines
Average Cost of a CNC Knife Cutting Machine
The price of a CNC knife cutting machine heavily depends on its size, specifications and features. For most industrial models that are high end and fully automated, prices can start from $15,000 to $30,000 while the cheapest ones can exceed a hundred thousand dollars. With a higher price tag also comes better technology integration in order to increase the cut precision, improve the build quality, cutting speed among other factors.
Expected returns from a Digital Cutting System
The investment required for the training, instillation for the presided machine should not be ignored, in order to gauge the investment expected returns on the cutting system. Use the estimates to total expenses in the ongoing operational tasks, maintenance, labor and energy. Proceed with the income earned via alteration in material consumption rate, enhancing productivity or expansion into new service areas. To work on an ROI assessment, on the basis of investment returns on digital cutting systems, the Net Earnings is divided by total investment and the result expressed in percentage terms. That way return on investment will help gauge and measure whether installing a digital cutting system is worth it.
Is it Economically Justified to Own Automatic Digital Cutting Machines?
When to purchase automatic digital cutting machines becomes a matter of addressing the requirements and the growth plans of a business. Most frequently these machines result in significantly increased productivity, increased precision and reduced manual labor due to automation processes. For businesses performing larger or more complicated cutting tasks, the first outlay can be integrated back into the company through enhanced productivity and safety. On the other hand, for smaller jobs or less frequent tasks, the initial outlay may not pay for itself in the short term. A detailed cost-benefit analysis developed around company’s goals and operational activities will be useful in establishing how worthwhile this investment will be.
Comparison: CNC Knife Cutting vs. Other Cutting Technologies
How Does CNC Cutting Compare to Laser Cutting Machines?
- Accuracy and Range Of Applications: Not only are CNC cutting machines able to work with thick and soft materials, which are difficult to machinelaser cutters thick and soft materials, but they also possess these characteristics: CNC cutting machines are versatile and can handle a multitude of materials.
- Material Resources: Some composite materials which have the tendency to burn might not be appropriate for laser cutting, but still can be used. Wood, foam, and even textiles can be used with the CNC cutters.
- Cost Of Operation: Compared to lasers which due to the regular need for source and optics maintenance demand are quite expensive devices, CNC machines have rather low maintenance and operating costs.
Advantages of CNC Over Traditional Cutting Methods
- Automation: The necessity of personnel is obliterated since the operation of the machinists will be replaced by the automatically controlled CNC cutting machines which enhances efficiency.
- Consistency: Since computers are used in the operation of the machines there is higher chances of avoiding human errors which in turn results to a higher consistency.
- Speed: CNC equipment have the capacity to make cutouts at a faster rate than manual work does, especially for intricate designs or bulky quantities.
- Customization: The requirement to work with different designs and to carry out numerous cuts between different designs without going through complex set up encourages mass customization and short runs.
When to Choose a Flatbed Digital Cutter Over an Oscillating Knife Cutter?
- Material Hardness: Extract more stringent materials cutting flatbed digital cutter for effective measure ensuring accurate cutting during the size and stability of the flatbed.
- Sheet Size and Layout: A flatbed cutter is ideal for large sheets or complex cutouts that would be easier to manage with a flatbed, when used.
- Production Volume: Where there is high volume or repetitive work that should be done with the same standards, flatbed digital cutters can be employed.
- Complex Cuts: For those precise and complicated cutting patterns that reap even better results than using an oscillating knife cutter.
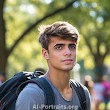