Running a construction site or any operation involving heavy machinery isn’t child’s play. These mighty beasts require constant care and attention to keep them roaring and performing at their best. Neglecting heavy machinery maintenance can lead to costly breakdowns, safety hazards, and a world of headaches for operators and site managers.
Luckily, this article provides six practical tips to make equipment upkeep easier. Read on!
Follow The Manufacturer’s Recommendations
One crucial practice for heavy equipment maintenance is following the manufacturer’s maintenance schedule. These recommendations come straight from the experts who designed and built your equipment. They know the ins and outs, the typical wear patterns, and the optimal maintenance intervals.
Think of it as changing the oil in your car – skip it, and you’re just asking for trouble down the road. But stick to that heavy equipment maintenance schedule, and your equipment will have a prolonged lifespan. Whether it’s quarterly lubrications, annual filter replacements, or regular inspections, these simple upkeep tasks are crucial.
Take construction equipment maintenance like excavators or cranes, for example. With their heavy workloads and exposure to the elements, regular maintenance is non-negotiable. So, whatever you do, prioritize routine maintenance according to your manufacturer’s instructions.
Keep Detailed Records
Detailed record-keeping is crucial for managing equipment upkeep. Note down every activity conducted on each piece of equipment, including the date, repaired or replaced parts, or oil changes.
Having this maintenance transcript is invaluable for multiple reasons. First, it allows for identification and traceability of your equipment’s health history., which enables you to pinpoint any recurring issues before they escalate.
Secondly, an extensive paper trail gives you rock-solid traceability if any hiccups or liability questions arise down the road. You’ll have a crystal-clear record of exactly what and when services were performed, creating an invaluable accountability trail.
The bottom line? Skimping on record-keeping is a rookie mistake. Document maintenance tasks, whether using sophisticated computer systems or good old-fashioned books.
Prioritize Operator Training
Your heavy equipment operators are your first responders for heavy machine care. They’re the ones in the trenches daily, with a front-row seat to spot any potential maintenance issues before they escalate. But are they empowered with the proper knowledge and skills?
Investing in comprehensive operator training pays massive dividends for preventive maintenance. This involves in-depth rundowns on pre-shift inspections, safe machine operating practices, and basic troubleshooting capabilities. Mastering these fundamentals is crucial for reducing unnecessary wear and tear on your machinery.
Take those pre-operation construction inspections, for instance. An operator well-versed in scanning for cracked hoses, checking brake fluid levels, and testing backup alarms can sidestep equipment breakdowns before they happen. They’ll be your early warning system for emerging issues.
Invest In Spare Parts Inventory
Every equipment manager’s goal is to avoid costly downtime, and maintaining a healthy supply of critical spare parts is vital. When machines go down, minutes of lost productivity increase quickly. But if you’ve stockpiled commonly replaced components like filters, belts, and lubricants on-site, your team can swap them out immediately for simple repairs.
Building this spare parts inventory is preventive planning at its finest. Review maintenance records to identify your machine’s frequent replacement needs, then order those essential spares in bulk to save costs and ensure sufficient stock. Utilize inventory management software and calculate reorder points to ensure you don’t run dry.
For example, if your trucking fleet relies on air filters, having a shelf full of spare parts lets replacements happen seamlessly with zero disruptive downtime. The bottom line is that spare parts stockpiling maximizes your equipment’s uptime and profits.
Leverage Technology
Robust inventory monitoring systems are game-changers that keep equipment running smoothly. These built-in digital co-pilots continually track vital signs such as engine performance, hydraulic oil and pressure, and coolant temperatures. In addition to gathering data, you also get instant alerts when any metric strays from the norm.
For example, instead of waiting for your company’s new excavator to show visible equipment issues, the monitoring system might ping you that hydraulic pressures are running high. You can then schedule a tune-up to avoid disastrous hydraulic failure down the line.
The best part is that many manufacturers now offer slick equipment maintenance software to centralize your whole equipment maintenance program. No more scattered paperwork – it automates scheduling, inventory tracking, and even operator notifications. Leveraging this cutting-edge technology gives your team a crucial edge in heavy equipment preventative maintenance care.
Develop A Preventive Maintenance Plan
Following the manufacturer’s basic recommendations is a good start, but true equipment longevity calls for a customized heavy equipment preventive maintenance strategy. This proactive approach accounts for the unique scenarios your machines operate in daily.
Preventive maintenance allows you to optimize service intervals and prioritize potential trouble areas specific to your operations. If you manage a fleet of trucks, for example, your plan might be to triple-check brake systems, considering the frequent stop-and-go driving.
An effective preventive maintenance plan focuses on two key elements: inspection frequency and machine maintenance specifics. Regular visual check-ins catch minor issues before they escalate, and outlined maintenance procedures cover all the bases, from fluid top-offs to filter swaps to belt adjustments.
Conclusion
Maintaining heavy equipment isn’t about following routines only; it’s about ensuring safety, efficiency, and longevity in your operations. Implementing these best maintenance practices enables you to establish a solid foundation for a comprehensive heavy-machine maintenance program. Remember, effective maintenance is an ongoing process, not a one-time fix. Regularly evaluate your program’s effectiveness, adapt to changing needs, and embrace new technologies to optimize your strategy continuously.
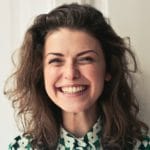