The choice of material has a significant impact on how a CNC machining work turns out. Metals and polymers have different advantages depending on their use. However, choosing CNC-machined plastic at the right time might result in weight reduction, cost savings, and more customization options. This article provides a comprehensive how-to for choosing the ideal material for your next project and looks at the primary benefits of machining plastics rather than metals.
Cost-Effectiveness
One of the main advantages of machining plastics rather than metals is cost effectiveness. Plastics like acrylic, nylon, polycarbonate, and polypropylene are usually less expensive than metals like titanium, stainless steel, and aluminum. In addition to raw materials, machining processes are also impacted by this cost difference:
- Tool Wear and Tear: Because plastics are softer than metals, cutting tools wear down less on them. This can reduce the frequency of tool changes and downtime.
- Quicker Machining Speeds: Plastics may often be machined at quicker speeds due to their lower density and resistance. Faster machining leads to shorter production times and lower labor costs.
- Simplified Operations: Post-machining procedures like annealing and surface polishing are rarely required for plastics, which reduces expenses. Metals are the opposite of this.
Since they enable businesses to lower material and operating costs without sacrificing functionality, plastics are a preferred substitute for prototypes or high-volume manufacturing.
Weight Reduction
In sectors like consumer electronics, automotive, and aerospace, where reducing bulk may boost efficiency and save operating expenses, weight is crucial. In this sense, plastics are clearly superior to metals:
- Reduced Density: Compared to metals, most polymers are substantially lighter. For instance, the density of polyethylene, a typical plastic, is around 1/8 that of aluminum.
- Energy Efficiency: By reducing the weight of plastic parts, machinery, and automobiles can use less energy, supporting long-term savings and sustainability objectives.
- Easier Handling: Manufacturing efficiency is increased when lightweight plastic components are simpler to move and assemble.
Choosing plastic that has been CNC machined is frequently the best option for applications where weight reduction is important.
Personalization and Adaptability in Design
When it comes to personalization and design possibilities, plastics provide unparalleled adaptability. In this regard, using CNC machining plastic is superior for the following reasons:
- Complex Geometries: Because plastics are less rigid than metals, it is easier to machine elaborate shapes, thin walls, and sharp corners without running the danger of causing structural damage.
- Broad Material Selection: Plastics are available in a variety of materials to satisfy certain needs like chemical resistance, UV stability, or electrical insulation. These materials range from transparent materials like acrylic to high-strength polymers like PEEK.
- Color Integration: Plastics may be produced in a range of colors, negating the need for secondary processes, in contrast to metals, which frequently need external coatings for aesthetics.
These characteristics make plastics perfect for uses like consumer goods, medical equipment, and customized industrial parts where distinctive or complex designs are needed.
Properties of Resistance and Durability
Although metals have historically been thought of as being strong, under some circumstances, contemporary polymers can provide durability that is on par with or even better. Among the main benefits are:
- Corrosion Resistance: Because plastics are naturally resistant to corrosion, they can be used in situations where they may come into contact with chemicals, water, or other harsh environments.
- Impact Resistance: Some plastics, such as polycarbonate, are very resistant to impact, which makes them perfect for safety gear and protective cases.
- Thermal and Electrical Insulation: In applications where controlling heat and electricity is crucial, plastics’ inherent insulating qualities can perform better than metals.
Manufacturers can attain desired performance metrics while avoiding some of the metals’ vulnerabilities, including oxidation or rust, by using the right plastic material.
Noise and Vibration Dampening
The fact that plastic can absorb vibration and noise better than metals is another advantage of CNC machining that is frequently disregarded. This feature is essential in applications like:
- Automotive Components: Cutting down on road and engine noise inside cars.
- Industrial Machinery: Reducing noise levels to enhance worker comfort and safety.
- Consumer electronics: lowering vibrations in gadgets like computers and cell phones to improve user experience. Given these benefits, plastics are a popular material for making operating systems that are smoother and quieter.
Sustainability and Recyclability
Sustainability is now a major factor in contemporary production. Metals can be recycled, but plastics are becoming more and more environmentally friendly.
Developments in recycled plastics and biodegradable polymers have improved these materials’ sustainability profile:
- Decreased Energy Needs: Plastics frequently demand less energy to produce and machine than metals, which helps to reduce carbon emissions.
- Recyclability: A circular economy is supported by the fact that many plastics may be recycled into new goods.
- Longer Lifespan: Because plastic components don’t break down easily in the environment, they often last longer between repairs.
Plastic CNC machining is a step toward more sustainable operations for businesses that prioritize green manufacturing.
Applications Where Plastics Outshine Metals
Although metals offer advantages, some applications obviously gain more from plastics’ special qualities:
- Medical Devices: Plastics that are biocompatible, sterile, and lightweight are ideal for prosthetics, surgical tools, and diagnostic equipment.
- Consumer goods: Plastics provide the perfect blend of durability and functionality in everything from lightweight eyeglass frames to robust smartphone casings.
- Automotive and Aerospace Parts: The lightweight nature of plastics improves fuel economy and lowers pollution.
- Food and Beverage Equipment: Processing and packaging equipment frequently uses non-corrosive, food-safe polymers.
Manufacturers can decide if plastics or metals are a better option by closely examining the needs of each project.
For applications requiring high strength and corrosion resistance, a titanium bar is an excellent choice over traditional metal options.
When Metals Are the Better Option
Even though plastics have many benefits, there are still situations in which metals are still the better option:
- Extreme Temperatures: Unlike most polymers, metals can withstand temperatures far higher than those that compromise their structural integrity.
- High Load-Bearing Applications: Because of their exceptional strength, metals are perfect for parts that are subjected to high loads or strains.
- Conductivity Requirements: Metals are unparalleled in applications that demand electrical or thermal conductivity.
Making decisions that are informed and suited to the demands of a particular project requires an understanding of these trade-offs.
Conclusion
The particular needs of each project will determine whether to machine metal or plastic. Plastics excel in applications that prioritize resistant qualities, weight reduction, cost savings, and design flexibility. However, metals are still essential for harsh conditions and demanding applications.
Using the benefits of CNC plastic machining, producers can create effective, affordable solutions that meet contemporary needs. Plastics’ adaptability guarantees their position as a key component of sophisticated manufacturing, whether it is in the production of complex medical gadgets, robust consumer goods, or lightweight aerospace components.
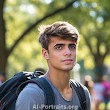