In today’s fast-paced consumer market, demand for safe, high-quality food products has never been greater. Faced with such demands, food manufacturers and packaging companies are looking to advanced inspection technologies more than ever.
Among all these technologies, x-ray inspection systems are significant in ensuring that the products reaching consumers are free from contaminants and meet the best-graded safety standards. This article discusses the relevance of quality control for food packages, the contribution of x-ray-controlled systems, and the relation of the density of the inspected products.
The Importance of Quality Control in Food Packaging
Quality control in food packaging is a multifaceted process. It guarantees that the finished product complies with industry standards, is safe to eat, and is free of defects. This procedure is necessary to protect consumers and uphold a brand’s integrity. A single contamination incident can lead to costly recalls. It can also lead to legal ramifications and severe harm to a business’s reputation.
Metal detection and visual inspection have traditionally played a significant role in food packaging inspection. However, these techniques have certain drawbacks. While effective, they cannot detect non-metallic contaminants or identify issues within the product, such as missing components or improper filling.
This is where advanced inspection technologies come into play. Systems that use X-rays are incredibly efficient compared to conventional techniques, as X-ray inspection delivers better precision and dependability. It is a necessary tool for modern food packaging operations.
How X-Ray Inspection Systems Work
X-ray inspection systems pass X-rays through the product as it passes through the production line, via a food conveyor. The detector records the X-rays, and based on the various degrees of absorption by different constituents within the product, the detector generates an image. Another software analyses this image and detects irregularities, including missing parts, foreign objects, or packaging flaws.
X-ray inspection is beneficial in the food sector, mainly because customers may have serious health problems if any toxins are present. One of its main benefits is the capacity of X-ray examination to identify a broad range of pollutants, including metal, glass, stone, bone, or any present polymers.
The Role of Density in X-Ray Inspection
A critical factor that affects the effectiveness of X-ray inspection is the actual density of a product under examination. Density means the mass amount in a specific volume of the product. It directly influences the way X-rays interact with the product’s material.
That means the denser the material in X-ray inspection, the more rays it absorbs, causing a darker picture to the detector. In contrast, less dense materials allow more X-rays to pass through and form a lighter image. The difference in absorption in the X-ray systems enables it to detect contaminants and inconsistencies within the product.
For example, a piece of bone in a chicken or a piece of glass in a jam may turn darker in the X-ray image, since these materials are denser than the food around them. The software of these systems can detect these anomalies and warn the operators about possible contaminants.
Product density affects the developed X-ray image and the inspection system’s calibration and sensitivity. For example, highly variable densities can cause images to overlap or create false positives, making it difficult to distinguish between natural product variations and actual contaminants.
Advanced X-ray systems use algorithms that compensate for these variations in density to provide clearer and more accurate images. Product size and shape may also affect how X-rays penetrate and are absorbed. Proper calibration and software adjustments are essential for optimising detection and minimising errors.
However, the density of the product itself can also pose challenges. Products of variable densities, such as a mixed fruit salad or a layered cake, can produce complicated images that require further analysis. Advanced X-ray systems, such as those provided by TDI Packsys, use powerful software capable of distinguishing between natural fluctuations in product density and actual contamination. Check them out to learn more about how density affects X-ray inspection.
Emerging Innovations
As the food industry evolves, new technologies are emerging to enhance quality and safety. One exciting development is the evolution of X-ray inspection technology, which employs artificial intelligence (AI) and an algorithm associated with machine learning. These improvements enhance the system’s ability to precisely discern between pollutants and product defects. AI-powered X-ray machines can learn from every inspection cycle, improving their detection skills and decreasing the probability of false positives and negatives.
Other development entails dual-energy X-ray systems that could use different sets of X-ray energy to differentiate between materials with similar densities but different atomic compositions. This would enable the detection of contaminants to be even more accurate and ensure that products with complex compositions are thoroughly checked.
Additionally, developments in X-ray sensor technologies improve the resolution of the images and the speed of processing, enabling fast and straightforward inspections without interfering with production speed. These new technologies are indeed significant steps towards food safety and quality control.
Endnote
In an industry where consumer safety is paramount, investing in advanced inspection technology is not a luxury but a necessity. X-ray inspection systems are essential in ensuring zero contaminants reach consumers. With these systems in place, manufacturers can ensure that the products delivered are the safest, high-quality, and ready to meet everyone’s expectations.
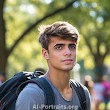