Flex-rigid printed circuit boards (PCBs) have revolutionized the design and functionality of modern electronic devices. These PCBs combine the benefits of both flexible and rigid PCBs, offering a versatile solution for a variety of applications. One of the most crucial areas where flex-rigid printed circuit boards (PCBs) have proven their value is in medical devices, where miniaturization, reliability, and performance are paramount. This case study explores the advantages of flex-rigid PCBs in the medical device industry, focusing on a specific application: implantable medical devices (IMDs). See also: PCBs.
Background: The Need for Miniaturization and Reliability in Medical Devices
The medical device industry is under constant pressure to produce smaller, more reliable, and more efficient devices that can be used in a wide range of patient care scenarios. In particular, implantable medical devices, such as pacemakers, neurostimulators, and drug delivery systems, must meet stringent requirements for performance, size, and durability. These devices often need to operate for many years inside the human body, where environmental factors such as heat, moisture, and movement can pose significant challenges.
Flex-rigid PCBs have emerged as a game-changer in this field, enabling engineers to design more compact, reliable, and functional devices. The integration of both rigid and flexible components allows for greater design freedom, making it possible to place components in areas that were previously inaccessible or difficult to manage with traditional rigid PCBs.
Case Study: Implantable Pacemaker with Flex-Rigid PCB
An example of the advantages of flex-rigid PCBs can be seen in a recent development of an implantable pacemaker used to regulate the heartbeat of patients with arrhythmias. Traditional pacemakers relied on bulky and rigid PCBs, which limited their overall size and functionality. With the adoption of flex-rigid PCB technology, the design of the pacemaker became significantly more compact while maintaining all necessary components for operation.
Flex-rigid PCBs enabled the pacemaker to incorporate flexible sections that could conform to the contours of the body, reducing the need for bulky connectors and minimizing the risk of failure due to movement or external stress. These flexible sections also allowed the device to better withstand the physiological motions of the human body, such as bending or twisting, without compromising performance or reliability.
Additionally, the rigid sections of the PCB provided a stable platform for critical components like the microprocessor, power supply, and communication modules, which require structural support. This hybrid design allowed for the optimization of both form factor and functionality, reducing the overall size of the pacemaker and improving its performance without sacrificing reliability.
Advantages of Flex-Rigid PCBs in Medical Devices
- Miniaturization and Space Efficiency: Flex-rigid PCBs allow for highly compact designs by combining both rigid and flexible layers. This makes them ideal for applications like pacemakers, which require both performance and miniaturization. By using flexible materials, the PCB can conform to irregular shapes and smaller spaces, freeing up valuable room for other critical components.
- Enhanced Durability and Reliability: In medical devices, especially implantable ones, durability and reliability are essential. Flex-rigid PCBs are more resilient to mechanical stress, such as bending, vibration, and shock, which are common challenges for devices exposed to the body’s movements. Their ability to flex and bend without breaking or degrading extends the longevity of the device, ensuring consistent performance over time.
- Reduced Interference and Improved Signal Integrity: Flex-rigid PCBs can be designed with integrated shielding and low-inductance connections, making them ideal for minimizing electrical interference. This is particularly important in medical devices like pacemakers, where precise electrical signals are critical to the device’s function. By reducing noise and improving signal integrity, flex-rigid PCBs contribute to the overall safety and effectiveness of the device.
- Cost Efficiency in Complex Designs: Although flex-rigid PCBs are often seen as a higher-cost option compared to traditional PCBs, they offer significant savings in the long term. Their ability to combine multiple functions and reduce the need for additional connectors, wires, or components can lower overall assembly and production costs. Furthermore, their enhanced reliability reduces the likelihood of costly device failures or recalls.
The integration of flex-rigid PCBs into implantable medical devices like pacemakers has proven to offer significant advantages in terms of size, durability, reliability, and performance. These PCBs allow for miniaturized designs that can withstand the stresses of the human body while maintaining high levels of functionality. As the demand for smaller, more efficient, and reliable medical devices continues to grow, flex-rigid PCBs will undoubtedly play an increasingly important role in advancing healthcare technology.
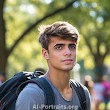