FMIS has been delivering industry-leading Asset Management systems for 35 years. Here are their reasons as to why it is important to change how you track and maintain assets.
There are numerous reasons why tracking and maintaining your assets is important to a business. Especially if your equipment, plant, machinery or IT assets are key to your infrastructure or customer service.
Efficiency
Greater efficiency in asset tracking is more than just spending less time on tracking your assets and equipment. Improving asset efficiency can improve utilisation, reduce acquisition costs and increase the useful life of your assets. Improving efficiency starts with asking a few simple questions. Do you know what assets you have? Do you know where they are? Do you know the condition of these assets?
Your answers to these questions will tell you how effective and efficient your current system is.
Knowing what you have
Your assets represent a large (if not the largest) investment for any business. A failure to properly track assets over their lifecycle leads to substantial additional costs for a business. Duplicate purchases, insurance premiums for ghost assets and unhappy auditors all stem from a failure to record purchases, transfers and disposals effectively.
An effective asset tracking system will allow you to see what assets you have. Increased visibility is essential to improving utilisation and cutting down on duplicated purchases.
Knowing where it is
Knowing what you have is good – but you also need to know where the asset is currently located. We have all had the experience of wasted hours trying to find a screen for that presentation to the board, and most offices have ‘that’ cupboard where office equipment gets dumped when no one knows quite where it belongs.
In fast-moving environments where tools, equipment and assets are regularly moving about, you can use barcode scanners (on your phone if you prefer) to record transfers and other actions.
The key to achieving a consistently accurate asset tracking system is to ensure that every user understands the importance of accurate tracking and that the process is as simple as possible. Can assignments be done directly from your phone? What processes can you automate or, even better, completely dispense with?
Knowing its condition
Remember that cupboard in the office that we mentioned, the one with all the equipment that didn’t have another home? The reason that most of those items ended up there in the first place is that they either didn’t work or were so out-of-date that they were effectively useless. A five-year-old laptop is not an asset. It is a waste of cupboard space.
Effectively managing an asset goes beyond knowing what you have and where it is. It requires an effective way to repair, dispose of and replace broken assets – also known as reactive maintenance. Regular preventative maintenance will also help to cut down on damaged or faulty assets and equipment.
Maximising the return on investment
Retain ad re-use
Companies that do not have effective asset tracking systems linked to effective purchasing controls will usually end up purchasing new assets when they already own the same item elsewhere that could be re-used.
Re-sale and disposal
Underutilised assets are a potential source of revenue. Clear visibility of what assets are being utilised will help to identify potential assets for disposal. This may be through re-sale, transfer to another business unit or just straight disposal.
Maintenance
There are a number of key reasons why asset maintenance is an important by-product of an effective asset tracking solution. Here are three key factors.
Accurate Valuation
Safety
Regular maintenance scheduling of work orders to check, calibrate, service, test or inspect equipment in the work environment is a key commitment to health and safety (HSE). Even something as basic as a PAT test needs to be scheduled and recorded.
Audit
With HSE, it isn’t enough to comply with the requirements. You need to be able to prove that you have done so. As much as an effective asset tracking system will help you to manage checks and maintenance more efficiently, it also creates an audit record that proves what has been done and when.
Reactive vs planned
The old saying ‘a stitch in time, saves nine’ is especially true when it comes to maintaining your assets. Regular maintenance will increase the useful life of most assets and can greatly reduce reactive maintenance costs further down the road.
Maintaining scheduled maintenance is only possible with effective tracking of assets and the creation of schedules for those assets to identify what needs to be done, by who, how and when.
Fixed Asset Depreciation
Depreciation calculations are often treated as a purely accounting function, but accurate depreciation calculations and forecasts are essential for planning capital expenditure and reporting accuracy. They also depend heavily on the accuracy of the asset register they are based on.
If an asset register is inaccurate, then depreciation will always be inaccurate to at least the same extent.
Leasing
The introduction of leasing standards such as IFRS 16 has greatly changed how companies manage their lease portfolios. Almost all leases now need to be treated as fixed assets or Right of Use (ROU) assets. For companies with a lot of leases, this change has complicated the process of tracking their leases and assets and often required specialist lease management systems.
Faster, cheaper and accurate
Despite the effort involved in implementing an effective asset tracking system, the benefits for businesses are substantial. Increased utilisation, cutting out wasted work hours and reducing asset costs make the effort well worthwhile.
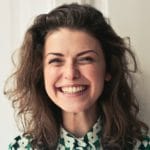