Condition monitoring has become an essential part of modern industrial maintenance strategies, helping companies detect potential machine failures before they result in costly downtime. Among the many tools used in predictive maintenance, vibration sensors play a pivotal role. These sensors continuously monitor equipment to detect irregularities, imbalances, misalignments, and other mechanical issues that can lead to failure if left unaddressed.
Understanding the different types of vibration sensors available and their applications is crucial to implementing an effective condition monitoring program. This blog explores the primary types of vibration sensors, their working principles, advantages, and how they contribute to maintaining machinery health.
What is Vibration Monitoring?
Vibration monitoring is the process of measuring vibration levels in machinery to assess its health and detect abnormal operating conditions. All rotating equipment, such as motors, pumps, compressors, and turbines, naturally produce some level of vibration. However, sudden changes in vibration patterns can indicate developing problems like:
- Bearing wear
- Shaft misalignment
- Imbalance
- Looseness
- Gear damage
By continuously tracking these vibrations, maintenance teams can perform repairs proactively, preventing unplanned downtime and extending machine life.
Importance of Vibration Sensors in Condition Monitoring
Vibration sensors are the core components that capture vibration signals, which are then analyzed to provide insights into machine performance. Reliable and accurate vibration sensing is critical to detecting early warning signs of mechanical failures.
Key benefits of using vibration sensors include:
- Early fault detection
- Improved equipment reliability
- Reduced maintenance costs
- Minimized unplanned downtime
- Enhanced safety
Different machines and operational conditions require specific types of vibration sensors. Choosing the right sensor depends on factors like measurement range, sensitivity, frequency response, and environmental conditions.
Common Types of Vibration Sensors
Let’s explore the main types of vibration sensors used in condition monitoring systems:
1. Accelerometers
Accelerometers are the most widely used vibration sensors in condition monitoring. They measure acceleration forces, which can be related to vibration levels.
Working Principle:
Accelerometers use the piezoelectric effect to convert mechanical motion into an electrical signal. When the sensor experiences vibration, a small crystal inside the sensor generates a voltage proportional to the acceleration.
Key Features:
- High sensitivity
- Wide frequency range
- Suitable for both low and high-frequency applications
Applications:
- Rotating machinery
- Bearings and gears
- Motors and pumps
Advantages:
- Highly reliable
- Capable of detecting both minor and severe faults
- Suitable for continuous monitoring
2. Velocity Sensors
Velocity sensors, sometimes called seismometers, measure the speed of vibration in a machine.
Working Principle:
Velocity sensors usually consist of a moving coil suspended inside a magnetic field. As the machine vibrates, the relative movement between the coil and magnet produces a voltage proportional to the velocity of the vibration.
Key Features:
- Measures vibration velocity, which is directly related to equipment health
- Typically used in industrial applications
Applications:
- Heavy rotating machinery
- Pumps, compressors, turbines
Advantages:
- Simple signal processing
- Useful for trending machine health over time
- Well-suited for medium to low-frequency measurements
3. Displacement Sensors
Displacement sensors measure the distance a machine part moves from its original position. These sensors are commonly used to detect shaft displacement, imbalance, and misalignment.
Working Principle:
Displacement sensors often use eddy-current technology. They generate a magnetic field, and as a conductive material moves within this field, the sensor detects changes in the magnetic flux, which correspond to displacement.
Key Features:
- Measures vibration amplitude in micrometers or mils
- Effective for low-frequency and slow-moving components
Applications:
- Shaft displacement monitoring
- Journal bearings
- Large turbines and compressors
Advantages:
- Very accurate for measuring small displacements
- Ideal for detecting misalignment and rotor position
4. Strain Gauge Sensors
Strain gauge sensors are less common in general vibration monitoring but are valuable for measuring strain and mechanical stress that may cause vibration.
Working Principle:
A strain gauge sensor measures the change in electrical resistance as a structure deforms under stress. This change is then converted into vibration or stress readings.
Key Features:
- Measures mechanical strain and vibrations
- Often used in structural health monitoring
Applications:
- Bridges, buildings, and large machinery structures
- High-stress rotating equipment
Advantages:
- Suitable for detecting material fatigue and potential failure points
- Can be customized for specific stress detection
5. MEMS Vibration Sensors
Micro-Electro-Mechanical Systems (MEMS) sensors are compact and cost-effective devices used for vibration monitoring in modern applications, especially for wireless condition monitoring systems.
Working Principle:
MEMS sensors use microfabricated structures to detect acceleration and vibrations. These structures deflect under vibration, changing capacitance that is measured and converted into a vibration signal.
Key Features:
- Compact and low-power
- Easy to integrate with wireless networks
Applications:
- Portable vibration monitoring devices
- IoT-enabled machinery
- Remote equipment
Advantages:
- Affordable and scalable for large deployments
- Suitable for real-time monitoring with wireless communication
- Growing use in smart factories and Industry 4.0 systems
Choosing the Right Vibration Sensor
When selecting a vibration sensor for condition monitoring, several factors must be considered:
- Frequency Range: The sensor must cover the vibration frequencies of interest.
- Amplitude Range: It should handle the expected vibration levels without saturation.
- Environmental Conditions: Sensors must withstand temperature, moisture, dust, and other challenging conditions.
- Machine Type: Different sensors are better suited for specific machines like high-speed motors, slow-moving shafts, or large turbines.
- Data Requirements: Determine whether continuous, real-time monitoring or periodic measurement is needed.
Selecting the right sensor type ensures accurate data collection and effective machine health monitoring.
Integration with Condition Monitoring Systems
Modern condition monitoring systems often combine vibration sensors with advanced data acquisition and analysis platforms. These systems can:
- Provide trend analysis
- Trigger alarms when vibration exceeds thresholds
- Integrate with wireless and IoT devices for remote monitoring
- Use AI and machine learning for predictive analytics
Wireless sensors and smart vibration monitoring systems are gaining popularity, as they reduce the need for hardwired installations and allow for scalable monitoring across large facilities.
Conclusion
Vibration sensors are essential tools for condition monitoring and predictive maintenance across various industries. Each type of vibration sensor — accelerometers, velocity sensors, displacement sensors, strain gauge sensors, and MEMS sensors — serves unique roles in detecting and analyzing machine health.
Accelerometers remain the most widely used due to their sensitivity and wide application range, while velocity sensors are favored for industrial machinery monitoring. Displacement sensors offer precise measurement of shaft movements, and MEMS sensors are opening new possibilities for wireless and cost-effective condition monitoring solutions.
Choosing the correct vibration sensor depends on the specific machine, environmental factors, and desired monitoring capabilities. When properly selected and integrated, vibration sensors significantly enhance the ability to detect potential failures early, optimize maintenance schedules, and improve overall equipment reliability.
By investing in the right vibration monitoring technologies, industries can move from reactive maintenance to proactive strategies, reducing downtime and ensuring safer, more efficient operations.
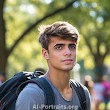