In high-performance manufacturing environments, material selection impacts every stage of production—from initial machining to the component’s service life. When the goal is to ensure dimensional stability, low deformation under load, and high resistance to surface damage, steel must meet a very specific set of requirements. For precision applications, hardened steel is often the most effective solution.
This type of steel is treated through heat processes that increase its internal strength and surface resistance. The hardening phase alters the microstructure, enhancing mechanical stability while maintaining the ability to withstand repeated stress. In sectors such as tooling, automotive, and die-making, this results in components that maintain performance even after prolonged exposure to friction, impact, and high loads.
The difference lies in how the material behaves over time. Hardened steel shows less wear, reduced micro-cracking, and greater resistance to dimensional changes caused by heat or pressure. These characteristics are particularly relevant for parts subject to continuous cycles or high-precision alignment, where failure or drift can compromise the entire system.
A deeper look into hardened steel properties reveals the technical depth behind these advantages. The hardness achieved through tempering directly affects wear resistance and tool compatibility. The depth of the hardened layer determines how the material reacts not just at the surface, but in its overall structural integrity. Thermal stability is another key parameter: when steel resists deformation under elevated temperatures, it remains reliable in environments where thermal expansion or fatigue could lead to inaccuracies.
Long-Term Performance through Informed Material Choice
Choosing hardened steel is rarely just about resisting wear. It also involves managing tolerances, surface finish, and how the material behaves during machining. A steel grade that is too hard may reduce machinability, causing tool wear or process inefficiencies. One that is too soft may meet production specs but fail prematurely in the field. This is where composition, treatment method, and intended application must be aligned with engineering goals.
In production lines where components operate under continuous or repetitive mechanical stress, using the correct steel grade helps reduce the need for corrective maintenance and improves process consistency. Over time, this supports a more predictable performance curve, extending both the life of the individual component and the systems it supports.
Hardened steel also plays a significant role in optimizing cost-efficiency over the full lifecycle of a product. While initial machining may involve more precise calibration and tooling, the durability achieved post-treatment helps offset these factors by minimizing replacement cycles. This is particularly relevant for manufacturers that depend on stable, repeatable outputs in tight timeframes and with high standards of quality control.
In applications where reliability cannot be left to chance, understanding the behavior of materials under real-world conditions is essential. Hardened steel stands out not just for its physical toughness, but for its ability to maintain those properties across diverse operating conditions. Its performance is the result of both metallurgy and process control—making it a material choice defined by results, not assumptions.
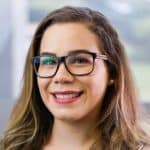