Business organisations, regardless of size, must focus on the safety of its employees and customers. In addition, these goals help firms achieve their legal requirements as well. Regular Portable Appliance Testing can help achieve all these goals. PAT Testing increases safety standards, helps companies become compliant with regulations, and, in turn, helps companies grow.
Routinely scheduled PAT testing can be the first step towards electric safety compliance. Electric shocks and fires are just some of the risks faulty devices pose to employees. Any company working with electrical devices can make living safer for their employees by simply scheduling testing for computing devices, kettles, pans, robots, and other machinery that needs to be electric. Regular PAT testing can solve and ensure all these risks are eliminated.
Making a profit by making employees feel safe should be the goal of any organisation. If companies are able to provide devices that have greater safety standards, employees will feel more relaxed and satisfied with their work making it a more desirable environment for everyone. Giving a dedicated priority to making all employees safe should be mandated across all organisations.
Reducing the Risk of Fire
You may or may not know this but faulty electrical equipment remains one of the top sources of fires in the workplace. Just a seemingly innocent fault in a cords, plugs or even internal wiring can have incendiary implications. That’s why PAT testing kits are made as they look for faults that are not sometimes visible with the eye.
It is safe to state that if testing is conducted regularly that would allow the businesses to avoid life threatening situations, only because defective goods can be fixed or exchanged on time. It is nothing short of a given that the resources spent on conducting PAT tests are marginal when estimated and compared to the commotion or reputation loss incurred because of having faced a fire at the premises.
Complying with Legal Obligations
An employer in the UK is under the law in making certain that the electrical appliances remain safe for use in cost at work regulations specifically the year of 1989. On the other hand, while there is no obligation to conduct PAT testing but it is recognized in most cases as the best approach to satisfying these set of requirements in relation to the specific law referring to electrical appliances safety.
One can incur criminal charges, get fined or the most extreme closure of business would help to state what not doing any efforts to make an appliance safe would do. Obtaining a PAT testing kit aids the business in complying since it gives a quick and simple technique to evaluating the company’s electrical equipment. The mere possession of records of PAT tests in itself will also be of aid in proving that the particular business is determined in ensuring that safety standards are always met.
Cost-Effectiveness and Longevity
Some business owners may conclude PAT testing costs them loss of money, however, it is rather a cost cutting element in the long term. The loss of mechanical and physical properties in electrical equipment are accurately noted, and this prolongs equipment’s life.
For example, wires and splints that are worn and weak can now be fixed as opposed to buying new equipments. In addition, businesses are able to prevent any unforeseen loss of time as a result of the breakdown of the equipment.
Enhancing Business Reputation
Safety-centered businesses are better positioned in the eyes of workers, clients as well as customers. With the increase in safety of the plant through compulsorily carrying out PAT testing shows the organization is professional and cares for its stakeholders.
In business types such as hospitality or retailing, where customers get exposed to electrical appliances on a regular basis, efforts such as attempting to enhance the safety threshold protects the customer and increases their loyalty. To illustrate, a café that carries out regular tests on its coffee machines, microwaves, and other appliances will provide a safe place for its staff and clients.
Decreasing the Difficulties with PAT Test Kits
The use of a PAT test kit has enhanced the testing procedures turn around time as well as assisted in ensuring that the tests are more streamlined. Aside from tools that facilitate the execution of tests, a majority of the kits are sold together with manuals. Many kits are designed for trained users, but some models are also intended for business owners or in-house maintenance staff.
Investing in a good azpat test kit makes it easier for businesses to carry out many inspections over a short period of time with minimal hassle. These days, many kits have meters with built-in memory that enable documentation of testing results, thus eliminating paper documents, while still ensuring access to documents for a compliance inspection.
How Often are PAT Tests Done
Depending on the kind of equipment used and the extent of usage the pat test frequency varies – the time between the tests for portable appliances in construction sites might be less than that for office equipment.
An evaluation of the risk factors of the workplace should guide businesses on how often to schedule testing. Speaking with specialists will make it easier to come up with a proper timetable and guidelines for testing that fit the testing requirements in the workplace.
Conclusion
Testing on a frequent basis using PAT testing is important in any organization as it addresses electrical safety concerns, legal obligations, and business needs. Spending money on an appropriate PAT testing kit and maintaining a regular testing timetable allows a business to safeguard its employees, mitigate dangers, and improve its image.
Making PAT testing a regular practice in the company is more than a compliance requirement– it is good business practice that demonstrates the company’s concern on safeguarding employees and enhancing their productivity.
Regular PAT testing ensures workplace safety, prevents electrical hazards, and helps businesses comply with UK regulations. Faulty appliances can cause fires, injuries, and downtime, impacting operations and reputation. pat testing kit simplify identifying issues early, extending equipment life and protecting employees and customers. Investing in PAT testing isn’t just compliance—it’s about safety, efficiency, and trust.
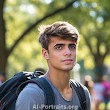