Warehouses are under constant pressure to move faster, reduce waste, and handle larger volumes with fewer errors. At the centre of this operational juggling act sits one quiet workhorse that rarely gets the credit it deserves: the pallet wrapping machine.
If you’re still manually wrapping pallets or relying on outdated systems, you’re likely losing time, money, and consistency every day. These machines don’t just tighten stretch film around a load. They streamline workflow, improve safety, and help ensure every product shipment leaves in top condition.
The Real Cost of Manual Wrapping
On the surface, wrapping pallets by hand might seem like a cost-saving move. No upfront investment, no training, just labour and stretch film. But when you break it down, the maths starts to tell a different story.
● Labour hours – Manually wrapping even a few pallets a day adds up quickly. What takes a machine two minutes can take a person ten.
● Injury risks – Repetitive bending, twisting, and pulling stretch film can cause strain injuries. This leads to higher injury claims, missed work, and lower morale.
● Inconsistent wrap – Human error leads to uneven film tension, loose loads, or wasted material. That impacts transport stability and increases product damage during transit.
● Film wastage – Hand wrapping often uses far more film than necessary. Machines can stretch film to its optimal limit, significantly cutting down usage.
Switching to automated or semi-automated pallet wrapping brings measurable improvements across the board. It’s not just about speed. It’s about control, consistency, and precision.
Types of Pallet Wrapping Machines and What They Do
Understanding what’s out there helps you choose the right fit for your warehouse. Pallet wrapping machines come in a few core types, each with its own advantages.
Turntable Wrappers
These are common in low to medium-volume operations. The pallet sits on a rotating platform while the film carriage moves vertically. It’s ideal for standard loads and straightforward operations.
Rotary Arm Wrappers
Instead of spinning the load, the arm rotates around the stationary pallet. This is better for unstable or very heavy items where spinning could cause shifting or tipping. It’s often used in higher volume warehouses.
Robotic Wrappers
These mobile units drive around the pallet to wrap it. They’re flexible, portable, and perfect for facilities with varied load sizes or limited floor space.
Ring or Orbital Wrappers
Designed for high-speed environments, these use a rotating ring to wrap stationary pallets very quickly. They’re more of a niche solution but excellent for high-volume, automated settings.
Choosing the right pallet wrapping machine depends on the volume, load type, floor space, and future growth plans of your warehouse. Investing in the right machine isn’t just about the short-term benefit. It’s about building capacity for tomorrow’s demand.
Efficiency Gains That Go Beyond the Wrap
Automating the wrapping process is about much more than wrapping. It opens the door to several valuable operational benefits.
Faster Throughput
Machines work at a consistent pace. Whether it’s the first pallet of the day or the last, there’s no slowdown. This keeps production and shipping lines moving without bottlenecks.
Better Load Stability
Properly tensioned, evenly wrapped pallets survive transport better. That reduces customer complaints, damaged goods, and returned shipments.
Reduced Film Costs
Machines use less film per wrap by stretching it more efficiently and avoiding overlaps. Over a year, this can translate into significant savings, especially in high-volume facilities.
Standardisation
With every load wrapped exactly the same way, quality control becomes easier. This consistency also makes it easier for transport teams to handle pallets safely and predictably.
Cleaner Work Environment
Machines reduce stray bits of film, excess roll ends, and manual messes. It leads to a tidier floor and a safer working space overall.
When Does It Make Sense to Automate?
Not every warehouse wraps enough pallets to justify a fully automated system. However, even mid-size operations benefit from switching to semi-automated machines. Here are a few clear signs it’s time to move on from manual wrapping:
● You wrap 10 or more pallets per day
● Workers regularly complain about the physical strain of wrapping
● You’ve noticed high film usage with lots of leftover waste
● Load stability issues are affecting delivery quality
● There’s a bottleneck in your dispatch process
If any of these sound familiar, it’s worth taking a closer look at automation options.
Key Considerations Before You Invest
Before diving in, it’s important to assess a few core factors to make sure the solution fits your warehouse’s layout and workload.
● Pallet size and weight – Not all machines can handle oversized or irregular loads, so match machine specs to your most common pallet types.
● Volume of pallets – Think about peak seasons and future growth. Go a little bigger than your current need if your volumes are rising steadily.
● Available space – Some machines need more room than others. A turntable model takes up less floor space than a rotary arm, for example.
● Power supply – Make sure your facility can handle the electrical load or if you’ll need adjustments for higher voltage machines.
● Training – Even simple machines require basic training. Factor in the time and cost to train staff properly.
● Maintenance – Like any mechanical equipment, ongoing maintenance is key. Check for support and service availability before committing.
Smart Warehousing Starts with the Basics
While high-tech inventory systems and complex automation often grab the spotlight, many of the biggest gains in efficiency come from focusing on fundamental tasks. Pallet wrapping is one of them.
Optimising something as routine as load wrapping can dramatically improve the daily rhythm of your warehouse. It cuts down on wasted time, wasted materials, and preventable injuries. It also gives your dispatch and logistics teams more confidence that every load will travel securely and arrive intact.
When you start automating simple, repetitive tasks like this, the ripple effect can be huge. Productivity improves. Costs go down. Staff satisfaction goes up. All from one solid piece of equipment doing one important job properly every time.
The Overlooked Upgrade That Pays Off
Many warehouse upgrades are flashy but short-lived. Pallet wrapping machines, on the other hand, quietly deliver real value every day. Once in place, they keep performing without fanfare or fuss.
If you’re aiming to build a more efficient, consistent, and scalable warehouse operation, this is one of the smartest places to start. It’s not just an equipment upgrade: it’s a shift toward smarter logistics from the ground up.
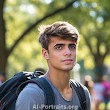