Automated replenishment is the established way to optimize inventory levels. This approach to inventory management leverages technology, real-time data, and forecasting algorithms to automate the process of restocking products or materials. By implementing an automatic replenishment system, businesses can ensure a continuous supply of inventory, minimizing stockouts and maximizing customer satisfaction. Let’s explore the best practices for implementing automatic replenishment.
Best Practices In Implementing Automated Replenishment
Implementing automatic replenishment in warehouse operations significantly boosts efficiency and profitability. This method offers enhanced inventory control by providing real-time visibility, which minimizes errors and maintains optimal stock levels, thus avoiding issues like overstocking or stockouts. It also increases operational efficiency by reducing the need for manual labor, freeing up employees to concentrate on tasks that add more value.
According to Statista, 13% of U.S. retail brands experienced inventory shrinkage of 3% or greater, while over 20% reported shrinkage between 2% and 2.99%. Inventory shrinkage, indicated by lost retail sales, usually stems from theft, operational errors, and systematic issues.
Automated systems improve demand forecasting by leveraging real-time data, which helps align replenishment strategies with historical sales trends and supply chain metrics. This optimization reduces carrying costs and helps manage inventory expenses more effectively, tracks expiration dates, and reduces waste.
1. Determining the Right Replenishment Strategy
Choosing the right replenishment strategy is crucial for the success of your automatic replenishment implementation. Your chosen strategy should align with your business’s specific needs, industry, and inventory management goals. Here are some commonly used replenishment strategies:
- Reorder Point Strategy: This strategy sets a minimum inventory level that triggers automatic replenishment when stock is low. It is ideal for fluctuating demand or high-velocity SKUs.
- Periodic Strategy: This method replenishes inventory at set intervals, regardless of stock levels, and is suitable for predictable demand cycles or slow-moving products.
- Just-In-Time (JIT) Strategy: JIT minimizes carrying costs by replenishing inventory to meet demand. It requires accurate forecasting and supplier coordination, which is common in industries with short lead times.
- Economic Order Quantity (EOQ) Strategy: EOQ helps businesses find optimal order quantities by balancing carrying and ordering costs to minimize total inventory management costs.
- Vendor-Managed Inventory (VMI) Strategy: VMI involves suppliers monitoring stock levels and initiating orders, requiring collaboration and real-time data access, streamlining replenishment, and reducing stockouts.
When selecting a replenishment strategy, it’s essential to evaluate your business’s unique requirements and constraints. Consider factors such as demand variability, lead times, product shelf life, and storage capacity to determine the strategy that best aligns with your goals.
2. Data Analysis and Forecasting
Accurate data analysis and forecasting are crucial for the successful implementation of automatic replenishment. Here are some best practices for data analysis and forecasting:
- Analyze historical sales data using statistical techniques like moving averages, exponential smoothing, and regression analysis to identify demand patterns and trends.
- Utilize demand forecasting techniques such as time series analysis, causal forecasting, and demand sensing to predict future demand accurately.
- Collaborate with key stakeholders to gather insights and improve forecasting accuracy by incorporating their expertise and market knowledge.
It is essential to regularly monitor actual sales data and compare it to forecasted demand. If any discrepancies or deviations are identified, adjust your forecasts accordingly. Continuous monitoring helps identify changing market conditions, demand patterns, or unforeseen events that may impact your replenishment plans.
3. Integration and Automation
Integration and automation play a crucial role in optimizing your automatic replenishment process. Here are some key considerations:
Ensure seamless integration between your automatic replenishment system and other critical systems such as your ERP, POS, and WMS. Integration enables real-time data sharing, accurate inventory tracking, and automated order generation. It also eliminates manual data entry and reduces the risk of errors or delays.
Automate the generation and processing of replenishment orders to minimize manual intervention and human errors. Configure your automatic replenishment system to set reorder points or trigger orders based on predefined thresholds. This automation streamlines the replenishment process, reduces lead times, and ensures timely restocking.
Implement real-time inventory visibility and reporting capabilities to monitor inventory levels, track order status, and identify potential bottlenecks. Real-time reporting enables proactive decision-making, allowing you to address issues promptly and optimize your replenishment processes.
Implement exception management protocols to handle unexpected events or deviations from the replenishment plan. Define rules and workflows for managing exceptions such as stockouts, delays, or quality issues. Exception management ensures that you can respond promptly to disruptions and minimize their impact on your inventory management.
4. Training and Change Management
Successful automatic replenishment requires adequate training and change management. Train employees on the new system, covering its features and benefits with comprehensive materials and hands-on workshops. Continuous education enhances adoption. Communicate the benefits to all stakeholders, address concerns, and provide ongoing support during the transition to ensure smooth implementation.
5. Monitoring and Continuous Improvement
Monitoring and continuous improvement are essential for maintaining optimal performance and maximizing the benefits of your automatic replenishment system. Here’s how to ensure ongoing success:
- Key Performance Indicators (KPIs). Define and track key performance indicators (KPIs) such as order fill rate, inventory turnover, stockout rate, and order cycle time to monitor the effectiveness of your automatic replenishment system. Regularly analyze these metrics to identify areas for improvement and implement corrective actions.
- Regular System Audits. Regularly audit your automatic replenishment system to assess performance, accuracy, and adherence to processes. Identify gaps and inefficiencies and implement corrective measures to optimize utilization and ensure compliance with best practices.
- Continuous Process Optimization. Continuously review and optimize replenishment processes by analyzing data, gathering customer feedback, and monitoring industry trends. Identify areas for improvement, such as order batching, lead time reduction, or supplier collaboration, and implement process enhancements to achieve operational excellence.
- Collaboration and Knowledge Sharing. Stay updated on automatic replenishment trends and best practices by participating in industry forums, conferences, and networking events. Collaborate with peers, suppliers, and technology providers to share knowledge and foster innovation, keeping your business at the forefront of industry developments.
For example, LEAFIO.AI’s analytics and reporting features provide businesses with comprehensive insights into their inventory management processes. The software enables quick identification of bottlenecks and problem areas, such as excess inventory and lost sales, allowing for data-driven decision-making. It promotes the accumulation and unification of inventory data, enhancing overall supply chain efficiency.
Conclusion
Implementing automatic replenishment in your warehouse operations is a strategic move that can revolutionize your inventory management processes. By following the best practices outlined in this comprehensive guide, you can optimize inventory levels, improve efficiency, and drive business success. Embrace the power of technology, data analysis, and continuous improvement to stay ahead of the competition and meet the ever-changing demands of the retail industry. With automatic replenishment as a cornerstone of your inventory management strategy, you can achieve sustainable growth, maximize profitability, and deliver exceptional customer experiences.
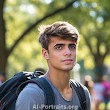