Ever found yourself staring at a row of gas cylinders, wondering which one actually belongs in your welding setup? It’s a scene many people know all too well—standing in a supply store, pretending to understand the labels while secretly hoping for divine intervention. But welding gases aren’t something to guess about. The right choice at https://www.tollgas.com/minneapolis-oxygen-supply/ can mean the difference between a smooth, clean weld and a mess that sends sparks flying in all the wrong directions.
Understanding the Role of Gas in Welding
Welding might look like it’s all about fire and molten metal, but it’s really a game of chemistry. The gas used doesn’t just protect the weld—it actively shapes how the process unfolds. Different gases affect penetration, arc stability, and spatter, and picking the wrong one can lead to weak joints or porosity that turns a solid weld into a brittle disaster.
In shielding gas welding, argon, carbon dioxide, helium, and oxygen often take center stage. Some welders swear by pure CO₂ for its deep penetration and affordability, while others lean toward argon-based mixes for a more controlled arc. Then there’s helium, often overlooked but unbeatable when welding non-ferrous metals like aluminum.
Choosing the Right Gas for the Job
Not all gases play well together, and not all metals respond the same way to every blend. When welding mild steel, a 75/25 argon-CO₂ mix is the go-to choice for clean welds with minimal spatter. But crank up the CO₂, and while penetration increases, so does the risk of a rougher weld that might need extra finishing work. Stainless steel demands something a bit more specialized—often a tri-mix of argon, helium, and CO₂ to maintain corrosion resistance and smooth bead appearance.
Aluminum is an entirely different beast. Pure argon usually does the trick, though helium can be added for higher heat input when welding thicker sections. It’s details like these that separate a functional weld from one that actually holds up under stress.
Cylinder Sizing and Handling—Because Running Out Mid-Weld Is Not an Option
Ever been in the middle of a project only to have the gas supply die out? It’s like the universe pressing pause at the worst possible moment. Choosing the right cylinder size is just as important as choosing the gas itself. Smaller cylinders work fine for occasional use, but if welding is a daily thing, constantly refilling tiny tanks turns into a frustrating cycle of wasted time and money.
Storage and safety matter just as much. Cylinders need to be upright, secured, and kept away from heat sources. And handling them? Never assume a cylinder is empty just because it feels light. A simple leak test with soapy water can reveal whether there’s a slow escape happening, preventing a surprise shortage down the line.
The Cost Factor—Balancing Quality with Budget
It’s tempting to go straight for the cheapest option, but when it comes to welding gases, cutting corners often leads to spending more in the long run. Industrial-grade gases come with purity levels that impact weld quality, and impurities can introduce porosity or contamination that weakens the final product. It’s a trade-off: lower-cost gas might work, but if it leads to rework, wasted materials, or an unreliable weld, is it really saving anything?
Refill strategies can also make a difference. Some suppliers offer cylinder exchanges, while others provide refills, and the price difference can be significant. Owning cylinders outright means long-term savings, but renting can be a better choice for those who don’t need constant access. Finding the right balance keeps the shop running efficiently without unnecessary expenses.
Keeping It Simple—Best Practices for Smooth Welding
With the right gas locked in, a few good habits make all the difference. Checking regulator settings before starting saves a lot of frustration. A flow rate that’s too high is just money floating into the air, while too little coverage leaves the weld exposed to contamination. Keeping hoses and fittings in good condition prevents leaks that might not be obvious until the weld starts acting up.
And here’s a pro tip: when shutting things down, always bleed the lines. It seems minor, but it extends the life of the regulators and prevents unwanted pressure buildup. It’s one of those small habits that pay off over time.
Final Thoughts—Why Gas Choice Matters More Than You Think
Welding isn’t just about melting metal together—it’s about control, precision, and knowing how to make each component work in harmony. The gas supply plays a bigger role than it gets credit for, and getting it right means stronger welds, less cleanup, and a smoother overall process.
So the next time there’s a choice between gas types, cylinder sizes, or suppliers, it’s worth taking an extra moment to think it through. The right decision can save time, money, and frustration while making every weld count.
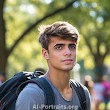