At the 2024 Advanced Manufacturing Minneapolis conference, Rahul Garg, Vice President of Siemens Industrial Machinery, delivered a keynote titled “Digitalization: The Key to Accelerating the Future of Manufacturing.” He discussed how manufacturers can address global competition, labor shortages, and the dual demands of innovation and sustainability through digital transformation. Below are the key points of his speech and the three core elements for manufacturers to achieve enterprise digitalization.
Challenges and Opportunities for Manufacturers
Rahul Garg pointed out that today’s manufacturing industry faces numerous challenges, including labor shortages, new customer demands for Equipment as a Service, and the growing industry automation and intelligence trend. Garg emphasized, “The current manufacturing model cannot meet future demands, and digitalization is the only solution to these challenges.”
He further explained that digitalized businesses combine the physical and digital worlds, helping companies optimize operations and create more value. Specifically, digitalization enables more efficient production line management, reduces equipment downtime, increases productivity, and lowers costs. For example, lifting equipment like overhead cranes and gantry cranes can leverage digital technologies for remote monitoring and predictive maintenance, helping manufacturers improve equipment lifespan and efficiency.
These smart crane systems integrate sensors and IoT (Internet of Things) technology, allowing real-time data transmission that provides detailed equipment performance analysis. This enables the early identification of potential failures and preventive maintenance, reducing unnecessary repairs and downtime. For instance, a digitally managed overhead crane can automatically adjust operational parameters based on load, work cycles, and environmental factors, ensuring optimal performance. Additionally, gantry cranes can make lifting operations more precise and efficient through integrated smart control systems, improving workplace safety.
Three Core Elements of a Digitalized Enterprise
Comprehensive Digital Twin
The digital twin is a digital representation of all physical entities within a business, including product design, production processes, and product performance during customer use.
- Product Design Simulation: Manufacturers can test and optimize mechanical designs, electrical simulations, and equipment operations in a virtual environment using 3D simulation technology. For example, the design of modern gantry cranes can be precisely calculated through digital simulations to reduce testing time and costs.
- Production Process Simulation: Digital twins can simulate the entire production process, helping businesses identify potential issues and optimize workflows before implementation.
- Customer Feedback Integration: Monitoring equipment performance in customer operations not only resolves customer issues but also improves future product designs.
Digital Thread
The digital thread connects all digital twins, streamlining and integrating all business capabilities into a unified process. Garg likened it to a subway map for businesses: “It allows seamless connections between different business processes, enhancing overall efficiency.” He also mentioned that the needs of each industry and customer vary, so the implementation of the digital thread requires high customization.
Industrial AI
Industrial AI accelerates the digitalization process through data-driven methods, from automating simple tasks to optimizing complex processes. AI is becoming an indispensable tool for the manufacturing industry.
- Task Automation: Using large language models and AI tools, repetitive tasks can be automated, improving productivity.
- Engineering Assistance: For example, AI assists PLC programmers in writing initial code, significantly improving development efficiency.
- Solving Complex Problems: AI provides innovative solutions by analyzing data, such as preventing production line shutdowns.
First Steps in Digital Transformation
Garg stressed that manufacturers need to take the following steps to begin their digital transformation:
- Establish a single source of truth to ensure data accuracy and consistency.
- Connect business processes through digital twins and digital threads.
- Leverage emerging technologies like AI to further optimize operations and product development.
He concluded, “Digitalization is not the future; it is the present. It will help businesses unleash collective intelligence, making them more efficient and competitive.”
Conclusion
Digital transformation is shaping the future of manufacturing. From product design to production optimization and customer service, digitalization offers unprecedented opportunities. In an increasingly competitive global environment, businesses must embrace digitalization to maintain a leading position. By applying it to manufacturing equipment, such as gantry cranes, manufacturers can complete complex projects more efficiently while utilizing digital twin technology to optimize equipment performance and reduce operational costs. This shift brings unprecedented flexibility and sustainability to the industry.
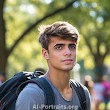