Introduction
In the world of manufacturing, CNC cutting and laser cutting are two popular methods used to achieve precision in shaping materials. While both methods serve the same purpose, they differ significantly in how they operate and their ideal use cases. This article aims to explore the differences between CNC cutting and laser cutting, helping you understand which might be better suited for your specific needs.
What is CNC Cutting?
CNC (Computer Numerical Control) cutting is a process that involves the use of computers to control machine tools such as lathes, mills, routers, and grinders. The process is highly versatile, making it suitable for a wide range of materials including metals, plastics, and wood. CNC cutting excels in precision, making it ideal for complex designs that require high accuracy.
- Advantages:
- Offers high precision in cutting.
- Can handle a variety of materials.
- Suitable for producing complex designs with consistent quality.
- Disadvantages:
- Slower for intricate patterns compared to laser cutting.
- Requires regular maintenance of tools.
What is Laser Cutting?
Laser cutting, on the other hand, uses a focused laser beam of the laser cutter to melt, burn, or vaporize material, resulting in a highly precise cut. This method is particularly effective for cutting materials like metals, acrylics, and certain fabrics. Laser cutting is known for its speed and the smoothness of its cuts, making it a go-to choice for intricate designs.
- Advantages:
- Provides extremely high precision.
- Faster cutting speeds for thin materials.
- Produces clean, smooth edges with minimal post-processing.
- Disadvantages:
- Limited by material thickness.
- Risk of heat distortion in some materials.
Comparative Analysis
- Precision:
- Both CNC and laser cutting offer high precision, but laser cutting is superior for extremely fine details.
- Speed:
- Laser cutting generally offers faster speeds, especially for thinner materials and intricate designs.
- Material Versatility:
- CNC cutting is more versatile in terms of the range of materials it can handle, including thicker materials.
- Cost:
- Laser cutting might be more cost-effective for small, intricate projects due to its speed and minimal waste, while CNC cutting can be more economical for larger or more diverse material requirements.
- Suitability for Complex Designs:
- Laser cutting is ideal for intricate and detailed designs, whereas CNC cutting is better for complex shapes in thicker or harder materials.
Applications and Industries
- CNC Cutting: Commonly used in industries such as automotive, aerospace, and woodworking for tasks like creating parts, molds, and custom furniture.
- Laser Cutting: Frequently used in industries such as electronics, fashion, and signage for tasks like cutting intricate patterns, engraving, and producing fine components.
Choosing the Right Cutting Method
When deciding between CNC and laser cutting, consider the following:
- Material Type: The laser cutting machine is better for thin, delicate materials, while CNC cutting handles a broader range of material thicknesses.
- Precision Requirements: If extremely fine details are needed, laser cutting is the preferred method.
- Production Speed: Laser cutting is generally faster, but CNC cutting might be more efficient for larger volumes or thicker materials.
- Budget: Your decision may also hinge on cost, with laser cutting being more cost-effective for small, detailed work and CNC cutting offering more versatility for larger projects.
Conclusion
Both CNC cutting and laser cutting are invaluable tools in modern manufacturing, each offering unique advantages depending on the project requirements. Whether you need the versatility of CNC cutting or the precision of laser cutting, understanding the strengths and limitations of each method will help you make an informed decision for your next project. For an in-depth understanding of how laser cutting performs in various applications, you can explore the results of an OMTech laser test, which showcases the precision and efficiency of laser technology in diverse materials.
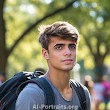