Custom Mylar bags are a choice, for packaging a variety of items, such as food, beverages, cosmetics and pharmaceuticals. Their durability, versatility and ability to maintain product freshness make them an excellent packaging option.. Have you ever thought about how these bags are printed with captivating designs and vibrant colors?
Lets explore the process of printing custom Mylar bags starting from the design phase to the outcome.
Understanding Mylar; The Basics
What is Mylar?
Mylar, a type of polyester film renowned for its strength, flexibility and barrier properties is widely used in fields, including packaging. Its protective features shield contents from moisture, oxygen and light when utilized in packaging applications. By using Mylar for packaging purposes products shelf life can be prolonged while preserving their quality.
Why Opt for Mylar in Packaging?
Mylar is a choice for packaging due to its resilience, adaptability and exceptional barrier attributes. Its customizable nature allows for top notch printing that enhances product visibility, on shelves. Whether you require a resealable pouch, stand up bag or pouch design options can be tailored to suit your requirements.
The Design Stage
Crafting the Design
The first step, in the printing process is creating the design. Graphic designers collaborate closely with the brand to craft artwork that embodies the brands essence and resonates with its target audience. The design includes components such as the logo, color scheme, text and other graphics that will be featured on the bag.
Preparing the Artwork
Once the design is finalized it must be readied for printing. This involves transforming the design into a format with printing equipment. The design is typically divided into layers each representing a color or aspect of the design. This stage ensures that the final print will be precise and vibrant.
Printing Technologies
Flexographic Printing
Flexographic printing, also known as flexo printing is an used method for printing custom Mylar bags. It utilizes relief plates made of rubber or photopolymer. These plates are wrapped around rotating cylinders on a printing press. When the Mylar film moves through the press ink is transferred from the plates to the film resulting in the printed design.
Advantages of Flexographic Printing
High Speed; Flexographic printing is a process making it ideal, for large scale production runs.
Versatility; It is capable of printing on materials such, as Mylar, paper and plastic.
Cost Efficient; Flexographic printing utilizes plates that can be reused leading to cost savings.
Rotogravure Printing
Rotogravure printing, also known as gravure printing is a technique used for printing Mylar bags. This process involves etching the design onto a cylinder. The ink fills the etched areas. When the Mylar film runs through the press the ink is transferred onto it. Rotogravure printing is recognized for its ability to create quality and intricate images.
Advantages of Rotogravure Printing
Excellent Quality; Rotogravure printing delivers detailed images making it perfect for designs.
Consistent Results; This method ensures uniform color quality and repeatability.
Longevity; The etched cylinders have a lifespan making them suitable for large scale production runs.
Digital Printing
Digital printing is a technique that has become popular for customizing Mylar bags. Unlike flexographic and rotogravure printing methods digital printing doesn’t rely on plates or cylinders. Instead it directly prints files onto the Mylar film. This approach offers flexibility. Enables quick modifications, to the design.
Benefits of Digital Printing
Fast Turnaround; Digital printing offers a setup time making it perfect, for short print jobs and fast modifications.
Personalization; It provides a way to customize and personalize designs.
Cost Effective for Small Runs; Digital printing is budget friendly for small production batches as it doesn’t require plates or cylinders.
The Printing Process
Pre Press Preparation
Before printing commences the Mylar film undergoes preparation. This involves cleaning the film to eliminate any dust or debris that could impact print quality. The film is then treated to improve its ink retaining capacity. This treatment may involve corona discharge or flame treatment increasing the films surface energy for better ink adhesion.
Ink Application
Ink is applied to the Mylar film based on the chosen printing method. Each color in the design is printed separately with the film moving through stations or cylinders, for each color. This layering process ensures an precise print.
Drying and Curing
Following ink application the film undergoes a drying or curing process. This step ensures ink adhesion to prevent smudging or smearing.
In flexographic and rotogravure printing the film is often passed through a series of rollers. For printing, UV or LED curing may be utilized to dry the ink.
Ensuring Quality
Quality control plays a role, in the printing process. Every batch of printed Mylar bags inspection to verify color accuracy, design alignment and absence of defects. This critical step guarantees that the final product aligns with the brands standards and meets consumer expectations.
Post Printing Procedures
Lamination
The lamination process involves adhering a layer of plastic to the printed Mylar film. This enhances bag durability and barrier properties while safeguarding the printed design from scratches and fading.
Cutting and Sealing
Following printing and lamination the film is cut into bags which are then sealed. Various features like zippers, tear notches and spouts are added as required to ensure functionality for end users.
Delivery
The concluding phase entails packaging customized Mylar bags for shipping. The bags are carefully boxed up for delivery to customers with quality checks conducted throughout to ensure adherence, to brand specifications.
BrandMyDispo’s support team is always available to help you along the way ensuring that your printed Mylar bags meet your needs.
In Summary
The process of designing custom Mylar bags involves a mix of creativity and technology. Each stage from the concept, to the product plays a vital role, in crafting packaging that not only safeguards your items but also makes them stand out on store shelves. Whether you opt for flexographic, rotogravure or digital printing methods understanding this process can assist you in making choices and achieving outcomes for your brand.
When it comes to crafting custom Mylar bags BrandMyDispo delivers top notch quality, personalization options and excellent customer service. By selecting BrandMyDispo you’re not just purchasing packaging – you’re gaining a partner committed to supporting your business growth. Why delay? Enhance your packaging strategy with BrandMyDispos printed Mylar bags today. Witness the impact firsthand.
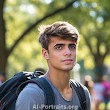