Downtime, especially unplanned, is a significant threat to any manufacturing operation. It can lead to substantial financial losses, disrupt schedules, and reduce overall efficiency. However, there are proven strategies to tackle this issue and drastically improve operational performance. Novacura has a huge expertise in supporting business processes with their unique solutions, offering effective tools to streamline operations and enhance productivity. Here are five effective ways to reduce downtime in manufacturing.
1. Optimize Production Execution
A key factor in minimizing downtime is optimizing production execution. Using a mobile solution like a Mobile Work Order app can greatly enhance the efficiency of production staff and work center operators. The apps like this enable real-time reporting and monitoring, leading to better analysis and decision-making.
The mobile app allows production staff to:
● Check task priorities based on the latest production plan.
● View task details, including technical documentation.
● Report operations (time/status) and used materials.
● Report and track downtime in real-time.
● Measure spending on downtime activities, including idle time.
For example, when a machine breaks down, the app allows operators to immediately report the issue, track the repair process, and record the downtime, providing accurate data for future analysis.
2. Limit Downtime Activities
Reducing the duration and impact of downtime activities is crucial. A special app can help work center operators save time and limit damages caused by inexperienced workers by streamlining maintenance tasks. Operators can:
● Request new tools or spare parts directly from the work center.
● Monitor the progress of these requests in real-time.
● Standardize maintenance tasks with guidelines.
● Complete maintenance checklists to ensure all steps are followed.
This system ensures that tools and parts are available when needed, reducing delays and preventing prolonged downtime.
3. Enhance Production Planning and Maintenance Integration
Integrating production planning with maintenance schedules is essential for minimizing unnecessary downtime. Real-time data feeds from each department provide planners with an accurate view of the factory, helping them react more quickly to issues.
Plan Maintenance Strategically:
● Visualize all planned production and maintenance activities.
● Shift maintenance schedules to align with production downtime.
● Limit disruptions caused by unexpected downtime.
By incorporating maintenance into production plans, companies can ensure that maintenance activities are performed during planned downtimes, avoiding interruptions during peak production times.
4. Implement Predictive Maintenance
Predictive maintenance is a proactive approach that uses data and analytics to predict when equipment might fail. By addressing potential issues before they become significant problems, manufacturers can prevent unexpected downtime. Use IoT and AI Technologies. Connect machines using IoT devices to monitor parameters such as power consumption, vibrations, temperature, and noise. This data can be analyzed using AI to:
● Provide historical data for analysis.
● Offer predictive analytics to foresee potential issues.
● Automatically escalate alerts if concerning trends are detected.
For example, a manufacturing plant implemented IoT sensors on their machinery to monitor vibration levels. When abnormal vibrations were detected, maintenance was scheduled before the machine failed, preventing a costly shutdown.
5. Enhance Communication and Data Collection
Effective communication and comprehensive data collection are crucial for minimizing downtime. Capturing and consolidating data from various departments allow for better decision-making and faster responses to issues. Use a digital solution to:
● Gather data from different departments, including the warehouse, shop floor, quality control, and maintenance.
● Provide real-time insights to measure downtime, identify root causes, and track performance.
● Use B2B portals for instantaneous communication with suppliers and customers.
For instance, a B2B portal for suppliers can confirm purchase plans and deliveries online, providing immediate notifications of delivery changes or delays. This allows manufacturers to adjust production plans accordingly, reducing the risk of downtime due to supply chain disruptions.
Reducing downtime in manufacturing is critical for maintaining productivity and profitability. By optimizing production execution, limiting downtime activities, integrating maintenance with production plans, implementing predictive maintenance, and enhancing communication and data collection, manufacturers can significantly reduce downtime and improve operational efficiency. Novacura has huge expertise in supporting business processes, providing tools that streamline operations and enhance productivity. By leveraging such expertise, companies can ensure a more efficient and resilient manufacturing process, minimizing downtime and maximizing output.
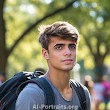