Imagine your hydraulic system failing right in the middle of a critical operation because of a substandard valve. You’d not only face downtime but also incur additional costs for repairs and replacements. By choosing high-quality hydraulic components, you enhance efficiency, reduce energy loss, and extend the lifespan of your equipment. These parts—like accumulators, pressure switches, and pumps—are essential for smooth operation and minimizing breakdowns. But how do you ensure you’re selecting the right hoses, fittings, and filtration systems? Let’s explore the factors that make a difference in the reliability of your hydraulic system.
Importance of Quality Parts
Choosing high-quality hydraulics parts is crucial because it ensures the efficiency and longevity of your hydraulic systems. When you invest in superior components, you’re directly enhancing performance efficiency. High-grade materials and precision engineering reduce friction and wear, optimizing fluid dynamics and reducing energy loss within the system. This translates to smoother operation and fewer breakdowns, thus extending the service life of your machinery.
Cost effectiveness is another key benefit of choosing quality parts. While the initial investment may be higher, the long-term savings are significant. High-quality components require less frequent replacements and maintenance, minimizing downtime and labor costs. Additionally, they’re less prone to catastrophic failures, which can lead to expensive repairs and operational halts.
Furthermore, premium hydraulic parts often come with better warranties and support services, giving you peace of mind. They meet stringent industry standards and undergo rigorous testing, ensuring they can withstand demanding operational conditions.
Types of Hydraulic Components
Understanding the different types of hydraulic components is fundamental to optimizing your system’s performance and reliability. Hydraulic systems rely on various components to function efficiently, including hydraulic accumulators and pressure switches.
Hydraulic accumulators store energy in the form of pressurized fluid, allowing your system to maintain consistent pressure and absorb shocks. There are different types of accumulators, such as bladder, piston, and diaphragm accumulators, each suited for specific applications. Properly selecting and maintaining accumulators can significantly enhance the efficiency and lifespan of your hydraulic system.
Pressure switches play a critical role in monitoring and controlling the pressure within your system. These devices activate or deactivate electrical circuits when specific pressure thresholds are reached, ensuring your system operates within safe parameters. Pressure switches come in various designs, including mechanical and electronic versions, each offering unique benefits depending on your system’s requirements.
Other essential hydraulic components include pumps, motors, valves, and filters. Pumps convert mechanical energy into hydraulic energy, while motors do the reverse. Valves control the flow and direction of the hydraulic fluid, and filters remove contaminants to protect other components.
Understanding these components and their functions is crucial for maintaining a robust and efficient hydraulic system.
Selecting Hydraulic Hoses
When selecting hydraulic hoses, it’s crucial to consider factors such as pressure rating, fluid compatibility, and environmental conditions to ensure optimal performance and longevity. Begin by evaluating the pressure ratings required for your system. These ratings must match or exceed the maximum operating pressure to prevent hose failure.
Consider the type of fluid being conveyed, as different hose materials offer varying degrees of compatibility with hydraulic fluids, oils, and other media. For example, synthetic rubber hoses are commonly used due to their flexibility and resistance to various fluids, while thermoplastic hoses provide superior chemical resistance and are lighter in weight. Always verify the hose material against the fluid’s chemical properties to avoid degradation and leaks.
Environmental factors, such as temperature and exposure to harsh conditions, also play a significant role in hose selection. High temperatures can degrade certain materials, so choose hoses rated for the specific temperature range of your application. Additionally, consider abrasion resistance if the hose will be exposed to rough surfaces or mechanical wear.
Choosing the Right Fittings
Selecting the appropriate hydraulic fittings involves understanding thread types, pressure requirements, and material compatibility to ensure leak-free connections and system integrity. You must first identify the thread standards applicable to your system. Common standards include NPT, BSP, and JIC, each with unique thread profiles and sealing methods. Ensuring the thread type matches your components is critical to preventing leaks and maintaining system efficiency.
Next, consider the pressure rating of your hydraulic system. Fittings are designed to withstand specific pressure ranges, and using a fitting with an inadequate pressure rating can lead to catastrophic failures. Always verify that the fittings you select meet or exceed the system’s maximum operating pressure.
Material compatibility is another crucial factor. Fittings are available in various materials such as steel, stainless steel, brass, and aluminum. Selecting a fitting material that’s compatible with the hydraulic fluid and the environmental conditions will prolong the lifespan of your system. For instance, stainless steel is often preferred for its corrosion resistance in harsh environments.
Understanding Hydraulic Pumps
Hydraulic pumps convert mechanical energy into hydraulic energy, providing the necessary flow and pressure to operate hydraulic systems efficiently. Selecting the right hydraulic pump for your system is crucial. You need to consider pump efficiency, which directly impacts overall system performance and energy consumption. A more efficient pump will generate the required hydraulic power with less input energy, reducing operational costs and heat generation.
Cavitation prevention is another critical factor. Cavitation occurs when air bubbles form in the hydraulic fluid, causing noise, vibration, and potential damage to pump components. To prevent cavitation, ensure your pump’s inlet pressure is sufficient and that the fluid is adequately filtered. Maintaining proper fluid levels and using the correct viscosity fluid also helps mitigate cavitation risks.
Furthermore, understanding the different types of hydraulic pumps—gear, vane, and piston—allows you to make an informed decision based on your specific application needs. Gear pumps are durable and straightforward, making them ideal for low-pressure applications. Vane pumps offer better efficiency and are suited for medium-pressure tasks. Piston pumps provide the highest efficiency and pressure capabilities, ideal for demanding industrial applications.
Role of Hydraulic Cylinders
To convert hydraulic energy into linear mechanical force, hydraulic cylinders play a critical role in driving actuators and executing precise movements within hydraulic systems. These components rely on pressurized hydraulic fluid to extend and retract a piston within a cylindrical housing, translating fluid power into mechanical work with high efficiency.
In terms of functionality overview, hydraulic cylinders are designed with several key parts: a cylinder barrel, piston rod, seals, and end caps. The cylinder barrel houses the piston, which moves back and forth as hydraulic fluid is directed into either side of the cylinder through ports. The seals ensure fluid doesn’t leak, maintaining pressure and system integrity.
Common applications for hydraulic cylinders span various industries. In construction, they’re essential in excavators and loaders for lifting and digging operations. Manufacturing sectors utilize them in pressing and molding machinery, where precise control over force and movement is crucial. Agricultural equipment like tractors and harvesters also rely on hydraulic cylinders for tasks like lifting heavy loads and steering.
When selecting hydraulic cylinders, consider factors like load requirements, stroke length, and operating pressure to ensure optimal performance and longevity. Properly chosen and maintained hydraulic cylinders contribute significantly to the efficiency and reliability of your hydraulic systems.
Essential Filtration Systems
Effective hydraulic systems rely heavily on robust filtration systems to ensure the purity of hydraulic fluid and prevent contaminants from compromising system performance and longevity.
The heart of any filtration system is its filtration efficiency, which dictates how effectively it can remove particulate matter and other impurities from the hydraulic fluid. High filtration efficiency is crucial for maintaining optimal contamination control, minimizing the risk of damage to critical components like pumps, valves, and actuators.
When selecting a filtration system, you must consider factors such as the micron rating, dirt-holding capacity, and beta ratio. The micron rating indicates the size of particles the filter can capture, while the dirt-holding capacity refers to the amount of contamination the filter can hold before requiring replacement. The beta ratio, a measure of filtration efficiency, quantifies the number of particles trapped by the filter compared to those passing through it.
Additionally, implementing multi-stage filtration can enhance overall system cleanliness by employing both coarse and fine filters. This layered approach ensures that larger contaminants are captured first, extending the life of finer filters downstream.
Prioritizing contamination control and investing in high-quality filtration systems will significantly reduce maintenance costs and enhance the reliability of your hydraulic systems.
Maintaining Seals and O-Rings
Proper maintenance of seals and O-rings is critical for ensuring the integrity and performance of hydraulic systems. First, you need to understand the seal materials in use. Common materials include Nitrile, Viton, and EPDM, each chosen based on compatibility with hydraulic fluids and operating conditions. Regularly inspect these seals for signs of wear, such as cracks, deformation, or hardening, which could compromise their effectiveness.
O ring lubrication is another key factor. Using the correct lubricant prevents friction and wear during operation. Typically, silicone-based lubricants are recommended, but always refer to the manufacturer’s guidelines for the best match. Misapplication can result in chemical incompatibility, leading to seal degradation.
Cleaning is also essential. Whenever you’re servicing hydraulic components, ensure that seals and O-rings are free from contaminants. Use appropriate cleaning agents that don’t damage the seal materials.
Additionally, correct installation is paramount. Improper fitting can cause immediate failure or shorten the lifespan of the seals. Always use the right tools and follow the manufacturer’s torque specifications to prevent over-tightening or under-tightening.
Benefits of Quality Valves
Just as seals and O-rings are vital for hydraulic system performance, investing in quality valves ensures reliable control over fluid flow and pressure regulation. High-grade valves offer enhanced durability, which reduces downtime and extends the lifespan of your hydraulic equipment. This durability is achieved through superior materials and precise manufacturing processes, ensuring that the valves can withstand the demanding conditions of hydraulic operations.
Quality valves also contribute to increased efficiency in your hydraulic system. They provide consistent and accurate control, minimizing energy loss and enhancing system responsiveness. This efficiency translates to better performance and lower operational costs, as the system requires less energy to achieve desired results.
Additionally, high-quality valves reduce the risk of leaks and pressure drops, maintaining optimal system performance and preventing costly repairs.
Regular Maintenance Tips
Regular maintenance of hydraulic systems is crucial to prevent unexpected failures and ensure optimal performance. Start by prioritizing fluid cleanliness. Contaminated hydraulic fluid can lead to component wear and system inefficiency. Ensure your system uses high-quality filters and regularly replace them according to the manufacturer’s specifications. Check fluid levels frequently and top up with the recommended hydraulic fluid to maintain the required viscosity and lubrication properties.
Next, focus on wear monitoring. Implement a routine inspection schedule to identify signs of wear on key components like pumps, valves, and actuators. Utilize diagnostic tools to measure performance metrics such as pressure, temperature, and flow rate. Deviations from standard readings can indicate wear or potential failures. Address these issues promptly to avoid costly downtime and repairs.
Additionally, inspect hoses and fittings for leaks or damage. Tighten connections and replace any components showing signs of fatigue or wear. Use torque wrenches to apply the correct force without over-tightening, which can cause damage.
Lastly, calibrate sensors and control systems periodically to ensure accurate readings and efficient operation. Regularly updating maintenance logs will help you track the health of your hydraulic system and plan for future maintenance activities effectively.
Conclusion
In hydraulic systems, quality components aren’t just an option—they’re a necessity. By investing in premium parts like durable hoses, reliable fittings, and efficient filtration systems, you ensure longevity and peak performance.
Remember, ‘a chain is only as strong as its weakest link.’ Don’t let subpar parts be that weak link. With proper maintenance of seals, O-rings, and valves, you’ll minimize downtime and enjoy cost savings in the long run.
Choose wisely, maintain diligently.
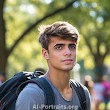