What is a CNC Machine Function?
CNC (Computer Numerical Control) machines are automated tools controlled by a computer to produce complex parts with high precision. The primary function of a CNC machine involves converting a digital design file into a physical component through various machining processes such as milling, turning, and drilling. This is achieved by inputting specific commands, known as G-code, which dictate the movement and operation of the machine’s tools. The CNC machine’s controller interprets these commands to precisely control the machine’s axes and cutting mechanisms, allowing for the creation of intricate geometries and tight tolerances that would be challenging to achieve manually. This automation not only enhances production efficiency but also ensures consistent quality and reduces the likelihood of human error.
View Goldsupplier CNC Machining more to get into the details
Understanding the CNC Machines
CNC machines are sophisticated devices essential to modern manufacturing, notable for their ability to execute highly precise and repeatable operations. At the core of CNC technology is the integration of computer systems to control mechanical movements, replacing manual intervention with a level of precision unattainable through traditional methods. The primary components of a CNC machine include the machine interface, controller, drive motors, and feedback systems.
The machine interface serves as the user interaction point, enabling operators to load job files and initiate machining processes. The controller functions as the brain of the CNC machine, interpreting G-code and translating it into signals that drive the machine’s movements. Drive motors, typically servo or stepper motors, are responsible for moving the machine components along multiple axes. Feedback systems ensure accuracy by continuously monitoring the position of the tools and making necessary adjustments.
The complexity and variety of CNC machines mean they can be applied to numerous materials such as metals, plastics, and composites, catering to industries from aerospace to medical device manufacturing. Understanding the operational fundamentals and components of CNC machines is crucial for optimizing their performance and achieving superior machining outcomes.
Types of CNC Machines Utilized in China
China’s manufacturing sector extensively employs a wide range of CNC machines, each tailored to specific applications and materials. The most commonly used CNC machines in this region include CNC milling machines, CNC lathes, CNC routers, CNC plasma cutters, and CNC laser cutters.
CNC Milling Machines
CNC milling machines are highly versatile, capable of cutting, drilling, and shaping workpieces with exceptional precision. These machines are employed across various industries, including automotive, aerospace, and electronics, to create intricate components and prototypes.
CNC Lathes
CNC lathes are primarily used for machining cylindrical parts. These machines rotate the workpiece against various cutting tools to perform operations such as turning, threading, and boring. CNC lathes are essential in producing components like shafts, pulleys, and bushings.
CNC Routers
CNC routers are employed mainly in woodworking, metal fabrication, and plastic cutting. These machines can cut, carve, and engrave materials, making them indispensable in industries such as furniture manufacturing and sign making.
CNC Plasma Cutters
CNC plasma cutters utilize a high-velocity jet of ionized gas (plasma) to cut through conductive materials like steel, aluminum, and brass. These machines are favored for their ability to produce clean and precise cuts, often used in metal fabrication and automotive repairs.
CNC Laser Cutters
CNC laser cutters employ a focused laser beam to cut through various materials with high precision and speed. These machines are ideal for applications that demand intricate and detailed cutting, such as electronics, medical devices, and customized signage.
The utilization of these CNC machines in China underscores the country’s commitment to maintaining a competitive edge in manufacturing through advanced technology and automation. Understanding the capabilities and applications of each CNC machine type is critical for optimizing production processes and achieving high-quality results.
Advantages of Using CNC Machines
The use of CNC machines in manufacturing offers numerous advantages over traditional manual machining methods. First and foremost, CNC machines significantly enhance production efficiency. With their ability to operate continuously and autonomously, they drastically reduce the time required to complete complex machining tasks. This leads to higher throughput and enables manufacturers to meet tight production schedules.
Secondly, CNC machines provide unparalleled precision and consistency. The digital control system ensures that each part is machined to exact specifications with minimal variance, resulting in superior quality products. This precision reduces material waste and minimizes the need for rework, thereby cutting down on production costs.
Moreover, CNC machines offer great flexibility in manufacturing. They can be easily programmed to perform a wide range of tasks, from simple cutting to intricate routing and engraving. This adaptability allows manufacturers to quickly switch between different production runs, making it easier to meet custom orders and adapt to market demands.
The use of CNC machines also enhances safety in the workplace. Automated operation reduces the need for manual intervention, lowering the risk of accidents and injuries associated with traditional machining processes. Furthermore, the enclosed environment of many CNC machines helps to contain dust, fumes, and other hazardous by-products of machining.
Additionally, CNC technology supports continuous innovation and improvement. With ongoing advancements in software and hardware, CNC machines continue to evolve, offering even greater capabilities and efficiencies. This ongoing development ensures that manufacturers can stay at the forefront of technological advancement, maintaining their competitive edge in the global market.
How to Choose a CNC Machining Service?
Factors to Consider in a CNC Machining Service
When selecting a CNC machining service, several factors need to be evaluated to ensure the chosen provider aligns with your specific manufacturing needs. The first consideration is the range of materials that the service can handle. Different projects may require metals, plastics, or composite materials, so the availability of a wide variety of materials enhances the service’s versatility.
Another critical factor is the precision and accuracy capabilities of the CNC machines. Ensure that the service provider uses advanced machinery capable of maintaining tight tolerances, as this directly impacts the quality of the finished product. Additionally, inquire about the lead times and their ability to meet your production schedule. Effective communication channels between your team and the service provider can also play a significant role in promptly addressing any issues that arise during the machining process.
Comparing Online CNC Machining Services
With the advent of digital technology, numerous CNC machining services now operate online, offering a convenient way to source your manufacturing needs. When comparing online CNC machining services, consider the platform’s user interface and ease of use. A streamlined ordering process can save time and reduce the likelihood of errors.
Furthermore, evaluate the transparency and comprehensiveness of the service’s quoting systems. An efficient service will provide detailed quotes that include all potential costs, such as setup fees, material costs, and shipping charges. Customer reviews and testimonials also offer valuable insights into the reliability and quality of the service.
Evaluating Quality CNC Services
Quality is paramount in CNC machining, and several indicators can help evaluate a service provider’s standards. Certifications such as ISO 9001 can be a good starting point, as they signify adherence to high-quality management practices. Additionally, examine the provider’s quality control measures, including the use of advanced inspection tools and protocols to ensure every part meets the specified requirements.
A robust support system is also crucial. Proactive customer support that offers troubleshooting, post-production services, and technical advice can make a significant difference in the overall satisfaction with the CNC service provider. By carefully evaluating these factors, you can select a CNC machining service that not only meets but exceeds your production expectations.
What Are the Types of CNC Machining Materials?
Common Materials Used in CNC Machining
CNC machining is versatile, accommodating a wide range of materials to suit various applications and industries. Commonly used materials include metals such as aluminum, steel, titanium, and brass, as well as plastics like ABS, polycarbonate, and nylon. The choice of material depends on factors such as mechanical properties, thermal stability, and the specific requirements of the final product.
Properties of Metal Parts vs. Plastic Parts
Metal parts and plastic parts each offer distinct advantages and disadvantages, influenced by their inherent material properties. Metal parts generally excel in strength, durability, and thermal resistance. For example, aluminum offers a good balance of strength and weight, while steel provides superior tensile strength and impact resistance. Titanium, though more expensive, is known for its exceptional strength-to-weight ratio and biocompatibility.
On the other hand, plastic parts bring benefits such as lighter weight, corrosion resistance, and ease of molding complex shapes. ABS is noted for its toughness and impact resistance, making it suitable for automotive parts and consumer electronics. Polycarbonate is highly transparent and has excellent thermal stability, while nylon offers good tensile strength and abrasion resistance. Choosing between metal and plastic depends largely on the specific application, environmental conditions, and cost considerations.
Wear and Corrosion Resistance in CNC Materials
Wear and corrosion resistance are critical factors in the longevity and performance of CNC-machined parts. Metals like stainless steel and titanium are renowned for their excellent corrosion resistance, making them suitable for harsh environments and applications involving exposure to chemicals or extreme temperatures. Hard metals like tool steels and hardened aluminum alloys exhibit superior wear resistance, essential for parts subjected to high stress and friction.
In contrast, certain plastics like PTFE (Teflon) and UHMW (ultra-high-molecular-weight polyethylene) offer exceptional resistance to wear and low-friction properties, making them ideal for applications requiring long-lasting, low-maintenance components. Additionally, the inherent corrosion resistance of plastics negates the need for protective coatings, simplifying production and reducing costs.
By carefully selecting materials based on wear and corrosion resistance, manufacturers can ensure the durability and reliability of CNC-machined components tailored to their specific application needs.
How to Start CNC Machining in China?
Getting Started with CNC Machining Setup
Setting up for CNC machining requires meticulous planning and precise execution. Initially, it is essential to identify the specific requirements of the project, including material selection, tolerances, and desired finishes. After finalizing these details, the next step involves acquiring and configuring the CNC machinery. This includes ensuring that the equipment is properly calibrated and equipped with the appropriate tools and fixtures for the task at hand. Additionally, developing a comprehensive CAD (Computer-Aided Design) model and generating the corresponding CAM (Computer-Aided Manufacturing) program will facilitate accurate and efficient machining operations.
Working with Custom CNC Machining Services
Collaborating with custom CNC machining services can significantly enhance the quality and efficiency of production. These services provide access to a wide range of materials, advanced machining technologies, and specialized expertise. When engaging with a custom CNC machining provider, it’s vital to communicate clearly the specifications and requirements of the component to be machined. This includes sharing detailed drawings, material preferences, and any post-processing needs. Establishing a solid relationship with the service provider can lead to improved lead times, cost savings, and superior final products.
Obtaining a CNC Machining Quote
To obtain an accurate CNC machining quote, several key details must be provided to the machining service. Start by submitting a comprehensive design file, preferably in a universally accepted format such as STEP or IGES. Include specific information about the material to be used, the desired quantity, and any critical tolerances or surface finishes. Additionally, outline any special requirements such as heat treatment or coating. The more detailed and precise the information provided, the more accurate the quote will be. A thorough quote will typically include costs for material, machining, labor, and any additional services, allowing for a transparent and informed decision-making process.
How to Maintain CNC Machined Parts?
Best Practices for CNC Part Maintenance
Effective maintenance of CNC machined parts ensures their longevity and reliable performance. Best practices include regularly inspecting parts for signs of wear or damage and cleaning them using appropriate solvents to remove debris and contaminants. Lubricating moving parts to reduce friction and prevent corrosion is also crucial. Additionally, adhering to the manufacturer’s guidelines for service intervals and using only recommended replacement parts can help maintain optimal functionality.
Importance of Regular CNC Machine Checks
Regular checks of CNC machines are essential for maintaining the quality and precision of machined parts. Routine inspections can help identify potential issues such as misalignments, worn components, or calibration errors before they lead to costly downtime or defective products. Performing these checks includes verifying the accuracy of tool calibrations, monitoring coolant levels, and inspecting filters and lubrication systems. Scheduled maintenance not only extends the machine’s lifespan but also enhances its performance and reliability.
Common Issues with CNC Machined Parts
CNC machined parts may encounter several common issues that can affect their performance and quality. These issues include dimensional inaccuracies due to tool wear or improper machine calibration, surface finish imperfections caused by inadequate cutting parameters, and material defects such as cracks or voids. Addressing these problems promptly through regular maintenance, precise machine setup, and the use of high-quality materials can significantly reduce their occurrence. By understanding and proactively mitigating these issues, manufacturers can ensure the consistent production of high-quality CNC machined components.
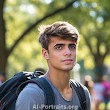