Plastic moulding technology has become a cornerstone of modern manufacturing, integral to producing a vast array of products ranging from everyday household items to advanced technological components. Among the global leaders in this industry, China has emerged as a dominant player, offering unmatched efficiency, quality, and cost advantages. This article delves into the multifaceted benefits of plastic moulding in China, making a compelling case for why global manufacturers should consider Chinese partners for their production needs.
I. Brief Overview of Plastic Moulding
Plastic moulding involves shaping plastic materials into desired forms using various moulding techniques such as injection moulding, blow moulding, and extrusion. These processes are essential in manufacturing industries, allowing for the mass production of complex shapes with high precision. Plastic moulding is critical in sectors like automotive, electronics, healthcare, and consumer goods due to its versatility and cost-effectiveness.
II. Introduction to China’s Role in Plastic Moulding
China’s rise as a manufacturing powerhouse has been nothing short of remarkable. Over the past few decades, the country has heavily invested in its industrial capabilities, positioning itself at the forefront of the plastic moulding industry. Today, China accounts for a significant share of the global plastic moulding market, thanks to its advanced technology, skilled workforce, and competitive pricing. Chinese plastic injection moulding manufacturers have successfully combined traditional craftsmanship with cutting-edge innovations, making them leaders in producing high-quality plastic products.
Chinese plastic moulding manufacturers examine technological advancements, cost efficiencies, quality standards, customization capabilities, and more, we aim to become an ideal destination for plastic moulding services.
III. Technological Advancements in Chinese Plastic Moulding
A. State-of-the-Art Machinery
Chinese plastic moulding manufacturers have embraced state-of-the-art machinery, investing in the latest technologies to enhance production capabilities. Modern injection moulding machines, for example, are equipped with advanced features such as precise temperature control, high-speed injection, and automated processes, ensuring high-quality outputs with minimal human intervention. These machines enable the production of complex and intricate designs with a high degree of accuracy and repeatability.
B. Innovation in Production Techniques
Innovation is at the heart of China’s plastic moulding industry. Companies continually explore new production techniques to improve efficiency and product quality. Techniques such as gas-assisted injection moulding and multi-component moulding are increasingly common, allowing for more intricate designs and reducing material usage without compromising strength. Additionally, advancements in mould-making technology, such as the use of 3D printing for rapid prototyping and mould fabrication, have revolutionized the industry by significantly reducing lead times and costs.
C. Impact on Product Quality
These technological advancements significantly impact product quality. High-precision machinery and innovative techniques lead to consistent and reliable products. Reduced defect rates and improved aesthetic qualities are direct benefits, which translate into higher customer satisfaction and brand reputation for businesses using Chinese moulding services. The integration of quality management systems and real-time monitoring ensures that each product meets stringent quality standards, thereby minimizing the risk of defects and recalls.
IV. Cost Efficiency
A. Competitive Labor Costs
One of the primary reasons purchasers flock to China is the competitive labor costs. Although wages in China have risen in recent years, they remain lower than in many Western countries. This cost advantage allows Chinese manufacturers to offer competitive pricing while maintaining high standards of production. The availability of a large and skilled labor force further enhances productivity and reduces overall plastic molding manufacturing costs.
B. Economies of Scale
China’s vast manufacturing ecosystem enables significant economies of scale. Large-scale production capabilities allow Chinese plastic moulding companies to produce vast quantities of products at lower per-unit costs. This scalability is particularly beneficial for companies looking to mass-produce products without compromising on cost efficiency. The ability to handle large orders efficiently and cost-effectively makes China an attractive option for businesses of all sizes.
C. Affordable Raw Materials
China’s access to affordable raw materials is another critical factor in its cost efficiency. The country’s extensive supply chain network and bulk purchasing power mean that raw materials for plastic moulding are readily available and cost-effective. This advantage is passed on to clients, resulting in lower overall production costs. The strategic location of raw material suppliers and the integration of supply chains ensure timely availability of materials, further reducing production delays and costs.
V. Quality Control and Standards
A. Rigorous Quality Control Measures
Quality control is paramount in China’s plastic moulding industry. Manufacturers implement rigorous quality assurance practices throughout the production process. These include regular inspections, testing at various stages of production, and stringent adherence to specified tolerances and dimensions. Advanced quality control tools, such as automated inspection systems and statistical process control, are used to ensure consistent product quality.
B. Compliance with International Standards
Chinese plastic moulding companies are well aware of the importance of meeting international standards. Many manufacturers possess certifications such as ISO 9001, ensuring that their production processes comply with global quality standards. This compliance guarantees that products manufactured in China can seamlessly integrate into international markets. Additionally, adherence to environmental and safety standards, such as ISO 14001 and ISO 45001, demonstrates a commitment to sustainable and safe manufacturing practices.
C. Case Studies of High-Quality Products
Numerous case studies highlight the high quality of products manufactured in China. For instance, multinational companies in the automotive and electronics industries have successfully partnered with Chinese plastic moulding firms, benefiting from high-precision parts that meet stringent industry standards. These partnerships have resulted in products that not only meet but exceed customer expectations in terms of quality and performance.
D. Case Studies – Auto Parts-Plastic Car Water Tank
As one of the important components of automobiles, the market for vehicle water tanks occupies an important position in the automobile industry. The car water tank mainly meets the needs of two aspects. One is that the auto water tank is an important part of the car, and it continues to increase due to the increase in car sales. The other is that the automotive water tank is a part that often needs to be replaced in car maintenance. This high quality auto water tank is made by China plastic moulding manufacturer – Sung Precision Mould & Plastic Co., Ltd .
VI. Customization and Flexibility
A. Tailored Solutions for Diverse Needs
Customization is a significant strength of Chinese plastic moulding manufacturers. They offer tailored solutions to meet the diverse needs of their clients, whether it involves unique product designs, specific material requirements, or particular production techniques. This flexibility ensures that manufacturers can obtain precisely what they need for their products. Chinese companies work closely with clients during the design and development phases to ensure that all specifications and requirements are met.
B. Examples of Custom Projects
There are numerous examples of successful custom projects undertaken by Chinese plastic moulding companies. For instance, a medical device manufacturer required a highly specialized plastic component with exacting standards. The Chinese partner developed a customized moulding solution, resulting in a product that met all regulatory and functional requirements. Similarly, an automotive supplier collaborated with a Chinese moulding company to develop a complex part with multiple material components, achieving both technical and aesthetic excellence.
C. Rapid Prototyping and Iteration
Chinese manufacturers excel in rapid prototyping and iteration. The ability to quickly develop and refine prototypes is crucial in today’s fast-paced market. Chinese plastic moulding companies leverage advanced prototyping technologies to produce and test prototypes rapidly, allowing for swift modifications and optimizations before full-scale production. This agility in product development helps businesses reduce time-to-market and stay competitive.
VII. Environmental and Sustainability Efforts
A. Green Manufacturing Practices
Sustainability is increasingly important in the plastic moulding industry, and Chinese manufacturers are no exception. Many companies have adopted green manufacturing practices, such as using energy-efficient machinery, minimizing waste, and implementing environmentally friendly production processes. These practices not only reduce environmental impact but also enhance the company’s reputation as a responsible and sustainable manufacturer.
B. Use of Recyclable Materials
The use of recyclable materials is a growing trend among Chinese plastic moulding companies. By incorporating recycled plastics into their production processes, manufacturers reduce their environmental footprint and promote sustainable practices. This approach aligns with global efforts to address plastic waste and pollution. Additionally, the development of biodegradable plastics and the use of renewable resources further contribute to sustainability.
C. Waste Reduction Techniques
Waste reduction techniques are integral to sustainable plastic moulding. Chinese manufacturers employ various methods to minimize waste, such as optimizing material usage, reusing scrap materials, and implementing precision moulding techniques. These efforts not only benefit the environment but also contribute to cost savings. Advanced waste management systems and recycling programs ensure that waste materials are efficiently processed and repurposed.
VIII. Challenges and Considerations
A. Potential Challenges in Sourcing
While there are numerous advantages to sourcing plastic moulding services from China, there are also potential challenges. Language barriers, cultural differences, and time zone discrepancies can complicate communication and project management. Additionally, ensuring intellectual property protection can be a concern for some companies. It is essential to understand and navigate these challenges effectively to maximize the benefits of partnering with Chinese manufacturers.
B. Tips for Successful Collaboration
To overcome these challenges, businesses should adopt best practices for successful collaboration. Clear and detailed communication, regular updates, and the use of bilingual project managers can help bridge cultural and language gaps. Conducting thorough due diligence on potential partners and understanding the legal landscape for intellectual property protection are also crucial steps. Establishing strong relationships and fostering mutual trust are key to successful long-term partnerships.
C. Mitigating Risks
Mitigating risks involves taking proactive measures to ensure smooth collaboration. Establishing clear contracts, setting realistic timelines, and maintaining open lines of communication are essential. Additionally, visiting manufacturing sites and conducting regular audits can help verify compliance with quality standards and contractual obligations. Engaging third-party inspection services and quality assurance experts can provide additional assurance and oversight.
IX. Future Outlook
A. Emerging Trends in Plastic Moulding
The future of plastic moulding in China is bright, with several emerging trends poised to shape the industry. Advancements in automation, the adoption of Industry 4.0 technologies, and the increasing use of bioplastics are some of the key trends that will drive innovation and efficiency. The integration of smart manufacturing technologies, such as the Internet of Things (IoT) and artificial intelligence (AI), will further enhance production capabilities and quality control.
B. Growth Opportunities
Growth opportunities abound in various sectors, including automotive, healthcare, consumer electronics, and packaging. As global demand for high-quality plastic products continues to rise, Chinese manufacturers are well-positioned to capitalize on these opportunities and expand their market reach. The development of new applications and markets for plastic products will create additional growth avenues.
C. Long-Term Benefits for Manufacturers
The long-term benefits of partnering with Chinese plastic moulding companies are substantial. Businesses can expect sustained cost savings, access to cutting-edge technologies, and the ability to produce high-quality, customized products at scale. These advantages will be crucial in maintaining competitiveness in an increasingly globalized market. The strategic partnerships formed with Chinese manufacturers will enable businesses to innovate, grow, and thrive.
X. Additional Resources
Contact Information for Leading Manufacturers To assist businesses in finding the right partners, here are some leading Chinese plastic moulding companies to consider:
1. Sung Precision Mould & Plastic Co., Ltd – Specializes in injection moulding for Plastic casings and everyday items.
2. Hubs – Known for custom moulding solutions and rapid prototyping services.
3. Rosti – Focuses on sustainable manufacturing practices and the use of recyclable materials.
FAQs:
1. What are the key factors to consider when choosing a plastic moulding partner in China?
Key factors include the manufacturer’s technological capabilities, quality control processes, cost efficiency, experience in the industry, and compliance with international standards. Also, consider communication ease and their ability to handle custom projects.
2. How can businesses ensure quality control when sourcing from China?
Ensure quality control by selecting manufacturers with rigorous quality assurance practices, obtaining certifications like ISO 9001, conducting regular inspections and audits, and using third-party quality assurance services.
3. What are the latest trends in the plastic moulding industry?
Latest trends include advancements in automation and Industry 4.0 technologies, increased use of bioplastics and sustainable materials, innovations in moulding techniques, and the integration of smart manufacturing technologies like IoT and AI.
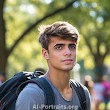