Microwave drying technology represents a significant advancement in the field of food processing and industrial drying. Unlike conventional drying methods, microwave drying employs electromagnetic waves to heat and evaporate moisture directly from within the material. This method offers numerous advantages, including faster drying times, improved energy efficiency, and enhanced product quality. By leveraging the unique properties of microwaves, this technology minimizes nutrient loss and flavor degradation, making it an attractive option for a variety of applications ranging from agricultural products to pharmaceuticals.view Leading Supplier Of Microwave Drying Equipment In China
What is Microwave Drying and How Does it Work?
Understanding the Basics of Microwave Technology
Microwave technology utilizes electromagnetic waves, specifically in the frequency range of 300 MHz to 300 GHz, to induce molecular motion within materials. This molecular agitation generates thermal energy resulting in the rapid heating of the material. The efficiency of microwave technology stems from its ability to transfer energy directly to the material’s water molecules, leading to uniform and volumetric heating. This direct interaction contrasts with traditional heating methods that rely on conduction and convection, which often result in slower and less consistent heating.Click here to read more
Comparison Between Microwave Drying and Conventional Drying Methods
Microwave drying offers several notable advantages over conventional drying methods. Traditional drying techniques, such as air drying and oven drying, rely on external heat sources to transfer thermal energy to the surface of the material, which then diffuses inward. This can lead to uneven drying, longer processing times, and higher energy consumption. In contrast, microwave drying heats the material from the inside out, significantly reducing drying times and energy usage. Additionally, conventional methods often result in significant nutrient loss and flavor degradation due to prolonged exposure to high temperatures, whereas microwave drying preserves these attributes by decreasing the overall heating duration and minimizing thermal gradients. View Loyal more to get into the details
Exploring the Mechanism Behind Microwave Drying
The mechanism behind microwave drying involves the interaction of microwave radiation with the water molecules within the material. When exposed to microwave energy, these polar molecules attempt to align themselves with the rapidly oscillating electromagnetic field, generating friction and heat. This process, known as dielectric heating, allows for efficient and targeted energy transfer. As the water molecules heat up, they transition into vapor, which is subsequently removed from the material. This internal heating mechanism ensures uniform drying and reduces the risks of surface hardening or case hardening, common issues encountered with conventional drying methods.
Advantages of Using a Microwave Dryer
Efficiency of Microwave Drying Equipment
Microwave drying equipment stands out due to its remarkable efficiency in material processing. The core advantage lies in the controlled and uniform heating it provides, resulting from the even distribution of microwave energy throughout the material. This efficiency translates to significantly reduced drying times and lowered energy consumption, making it a cost-effective solution for industrial applications. The precision of microwave drying further allows for the retention of critical properties such as texture, color, and nutritional value, which are often compromised in traditional drying methods. Consequently, industries benefit from higher quality end-products while also achieving operational cost savings.
Controlled and Uniform Heating in Microwave Drying
One of the most notable features of microwave drying is its ability to deliver controlled and uniform heating. Unlike conventional methods where heat is applied externally, microwave drying generates heat internally, ensuring an even temperature distribution across the material. This uniform heating mitigates the risks associated with traditional drying, such as surface hardening and non-homogeneous moisture content. Additionally, microwave systems can be easily regulated to maintain specific temperature settings, accommodating a diverse range of materials and drying requirements. This adaptability ensures optimal drying conditions, enhancing overall process efficiency and product quality.
Innovative Applications of Industrial Microwave Dryers
Industrial microwave dryers are being utilized in innovative ways across various sectors due to their versatility and efficiency. In the food industry, microwave drying is used to produce high-quality dried fruits, vegetables, and herbs, preserving their nutritional value and flavor. In pharmaceuticals, it facilitates the precise drying of heat-sensitive compounds, ensuring their stability and efficacy. Additionally, in the chemical industry, microwave dryers expedite the drying of powders and granules, optimizing production workflows. The technology is also being explored in the textile industry for the efficient drying of fabrics and yarns. These applications highlight the broad utility of microwave dryers, paving the way for advancements in diverse industrial processes.
Factors to Consider When Choosing a Microwave Drying Machine
Temperature Control Features in Microwave Drying Systems
Temperature control is a critical feature in microwave drying systems, directly influencing the quality and efficiency of the drying process. These systems are equipped with advanced temperature monitoring sensors and controllers that ensure real-time adjustments to maintain optimal drying conditions. The precision of these controls helps in preventing overheating or underheating, which could otherwise compromise the integrity of the material being dried. Sophisticated temperature control mechanisms also support energy conservation, as the system can operate at the minimal required energy levels. Such meticulous control is particularly advantageous when dealing with sensitive materials, allowing for consistent and repeatable results.
Benefits of Microwave Drying for Pharmaceutical Industry
The pharmaceutical industry significantly benefits from microwave drying technology due to its precise and efficient drying capabilities. Microwave drying ensures uniform moisture removal without subjecting the compounds to excessive heat, thereby preserving the stability and efficacy of heat-sensitive drugs. This method accelerates the drying process, reducing the time required compared to conventional drying techniques. Furthermore, the controlled environment of microwave drying minimizes the risk of contamination, which is crucial in maintaining the purity of pharmaceutical products. The reliability and precision of microwave drying also facilitate compliance with stringent industry standards, ensuring high-quality outcomes in pharmaceutical manufacturing.
Industrial Microwave Systems for Food Processing
Industrial microwave systems are revolutionizing food processing by providing a rapid, efficient, and controlled drying method. These systems are widely used to dry fruits, vegetables, and herbs, ensuring that the finished products retain their nutritional value, flavor, and color. The quick drying process helps in preserving the bioactive compounds and essential nutrients that are often lost in traditional drying methods. Additionally, microwave drying allows for the consistent production of high-quality food products, thereby meeting the demands of both consumers and regulatory bodies. With the ability to handle large volumes and varied types of food materials, industrial microwave systems are becoming an integral part of modern food processing operations.
Common Challenges and Solutions in Microwave Drying
Addressing Issues Related to Microwave Leakage
Microwave leakage is a significant concern in industrial microwave drying systems, as it can lead to safety hazards and reduce the efficiency of the drying process. To address these issues, preventative maintenance and regular inspection of microwave systems are paramount. Ensuring the integrity of the microwave cavity, door seals, and waveguides can minimize the risk of leakage. Additionally, employing leakage detectors and safety interlocks further enhances the security of the drying operations, safeguarding both personnel and equipment. Implementing these measures helps maintain optimal performance and compliance with safety standards.
Optimizing Microwave Power for Efficient Drying
Optimizing microwave power is essential to achieve efficient drying in industrial processes. The key lies in striking a balance between sufficient power to ensure rapid drying and avoiding excessive power that could damage the product or reduce energy efficiency. Power settings should be calibrated based on the specific properties of the materials being dried, such as their moisture content, density, and thermal sensitivity. Advanced control systems and real-time monitoring can aid in dynamically adjusting the power levels to maintain consistent drying and energy usage, leading to improved overall efficiency.
Ensuring Proper Temperature Control in Microwave Drying Process
Temperature control is crucial in microwave drying to prevent overheating and ensure uniform drying throughout the material. Accurate temperature sensors and feedback mechanisms should be integrated into the drying system to continuously monitor the temperature of the material. By employing precise temperature regulation, it is possible to maintain an optimal drying environment that preserves the quality and integrity of the product. Additionally, the use of computational models to predict temperature profiles can enhance the control strategies, ensuring consistent and reliable drying outcomes in industrial applications.
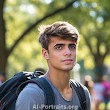