In today’s highly competitive manufacturing landscape, precision is paramount. Custom CNC machining services have emerged as a pivotal solution for producing intricate and accurate components, tailoring to the exact specifications of various industries. This blog delves into the essential aspects of custom CNC machining, exploring how advanced technology and expert craftsmanship converge to deliver unrivaled precision and quality. From understanding the fundamentals to examining real-world applications, we aim to provide a comprehensive overview that underscores the significance of custom CNC machining in modern manufacturing. Whether you’re an industry veteran or new to the field, this article will equip you with valuable insights into the capabilities and advantages of CNC machining for precision parts.
View Custom CNC Metal Machining Service From China for more details
What to Expect from Custom CNC Machining Services
Understanding the Custom CNC Machining Process
Custom CNC (Computer Numerical Control) machining is a manufacturing process that utilizes computerized controls and automated machinery to produce highly precise and intricate parts. The process begins with the creation of a digital 3D model or CAD (Computer-Aided Design) file, which serves as the blueprint for the part. This model is then converted into a CAM (Computer-Aided Manufacturing) program, which generates the instructions for the CNC machine.
Once the program is loaded into the CNC machine, the machining process can commence. This involves securing the raw material onto the machine bed or in a chuck. The machine then follows the programmed instructions, using various cutting tools to remove material and shape the part according to the design specifications. During this process, the CNC machine makes use of multiple axes of movement, allowing for complex geometries and tight tolerances to be achieved.
Real-time monitoring and feedback systems ensure precision and consistency, automatically making adjustments to maintain accuracy. The end result is a component that meets stringent quality standards and exact design requirements. This process is not only efficient but also scalable, making custom CNC machining an ideal solution for both prototypes and large production run. View ETCN more to get into the details
Advantages of Custom CNC Machining for Your Project
Custom CNC machining offers numerous advantages when it comes to producing precision parts for your project. One of the primary benefits is the high degree of accuracy and repeatability that CNC machines provide. By utilizing computer-controlled instructions, these machines can achieve extremely tight tolerances, which are essential for applications demanding precise measurements. Additionally, custom CNC machining is highly versatile, capable of working with a wide range of materials including metals, plastics, and composite materials. This flexibility makes it suitable for diverse industries such as aerospace, automotive, medical, and electronics. Moreover, the automation inherent in CNC machining allows for faster production times and reduced labor costs, ultimately enhancing both productivity and cost-efficiency. Real-time monitoring and automated quality checks ensure that each part conforms to the specified dimensions and quality standards, thereby minimizing waste and reducing the likelihood of errors.
Custom CNC Machining vs. Standard Machining: The Differences
- Accuracy and Precision: Custom CNC machining can achieve tighter tolerances and higher precision compared to standard machining techniques. This is due to the computerized controls that guide the machining process, ensuring consistent and reliable results.
- Complex Geometries: While standard machining is often limited by the capabilities of manual tools and operator skill, custom CNC machining can produce complex geometries and intricate designs with ease. The multi-axis movement of CNC machines enables the creation of detailed and sophisticated parts.
- Material Versatility: Custom CNC machines can handle a broader range of materials more effectively than standard machining methods. From hard metals like titanium to softer materials like plastics, CNC machining provides the flexibility to work with various substrates.
- Scalability: Custom CNC machining is highly scalable, making it suitable for both small prototype runs and large-scale production. This capability allows businesses to quickly move from concept to production, meeting project timelines and demands more effectively.
- Automation and Efficiency: Unlike traditional machining, which relies heavily on manual labor, CNC machining processes are automated. This not only speeds up production but also reduces human error, leading to more efficient and reliable manufacturing cycles.
Choosing the Right CNC Machining Materials for Your Parts
Metal and Plastic Options for CNC Machined Parts
The selection of materials in CNC machining is a critical decision that impacts the performance, cost, and application of the final product. Metals and plastics are the most commonly used substrates, each offering unique benefits and characteristics.
Metal Options
- Aluminum: Known for its lightweight and excellent machinability, aluminum is widely used in aerospace, automotive, and consumer electronics industries. It also offers good corrosion resistance and strength-to-weight ratio.
- Steel: With various grades available, steel provides versatility in machinability, strength, and hardness. It is commonly used in industrial machinery, automotive components, and construction materials.
- Titanium: Renowned for its high strength, low weight, and corrosion resistance, titanium is ideal for aerospace and medical applications. Its machinability is more challenging, but CNC machining provides the precision required for these high-performance parts.
- Brass: Valued for its easy machinability, corrosion resistance, and aesthetic finish, brass is frequently used in plumbing, electrical, and decorative applications.
Plastic Options
- Acrylic (PMMA): Offering excellent optical clarity and easy machinability, acrylic is commonly used in lighting, displays, and transparent enclosures.
- Polycarbonate: Known for its high impact resistance and strength, polycarbonate is used in safety equipment, automotive components, and electronic housings.
- Nylon: Providing good mechanical properties and wear resistance, nylon is suitable for gears, bearings, and other mechanical parts.
- Delrin (POM): With high stiffness, low friction, and excellent dimensional stability, Delrin is often used in precision components, automotive parts, and consumer products.
How Material Choice Impacts the CNC Machining Process
The choice of material significantly affects the CNC machining process, particularly in terms of tool selection, machining speed, and post-processing. Harder materials like titanium may require specialized cutting tools and slower machining speeds to achieve the desired precision and surface finish. In contrast, softer materials like aluminum and plastics can be machined at higher speeds but may necessitate careful handling to avoid deformation or surface damage.
Material properties such as thermal conductivity, hardness, and tensile strength also influence the selection of coolant and lubrication strategies to optimize the machining process and extend tool life.
Custom CNC Parts: Metal and Plastic Parts Considerations
When designing custom CNC parts, several factors should be taken into account to align with the specific requirements of the application:
- Mechanical Properties: Assess the strength, flexibility, and durability needed for the part to ensure that the material chosen can withstand the operational stresses.
- Thermal Properties: Consider the operating temperature and thermal conductivity requirements, especially for high-temperature environments.
- Electrical Properties: For electrical and electronic components, evaluate the material’s insulation properties and resistance to electrical currents.
- Aesthetic Requirements: Surface finish and visual appearance can be crucial for consumer-facing products, necessitating materials that can be easily polished or finished.
- Cost-Effectiveness: Balancing the material cost with performance requirements is essential to optimize the overall production cost and efficiency.
By carefully selecting the appropriate material and understanding its implications on the CNC machining process, manufacturers can achieve high-quality, reliable, and cost-effective custom parts tailored to specific applications.
From Prototypes to Production Parts: The CNC Machining Journey
Transitioning from CNC Prototypes to Full-Scale Production
Transforming an initial prototype into a full-scale production part is a critical phase in CNC custom parts manufacturing. This journey involves several steps focused on refining the design, optimizing the manufacturing process, and ensuring consistent quality and performance across high volumes.
Prototype: The First Step in CNC Custom Parts Manufacturing
The development of a prototype is the initial step in realizing a custom CNC part. During this phase, the focus is on validating the design, functionality, and material choices. Rapid prototyping techniques, such as 3D printing or initial CNC runs, allow for quick iterations and refinements based on testing and feedback. This stage is crucial for identifying potential design flaws and making necessary adjustments before moving to production.
Scaling Up: Manufacturing Process for High-Volume CNC Parts
Once the prototype has been validated, the challenge shifts to scaling up the manufacturing process for high-volume production. This step involves several critical processes:
- Process Optimization: Fine-tuning the machining parameters, such as spindle speed, feed rate, and tool path, to ensure efficient and consistent production. This may also involve automating certain aspects of the process to reduce human error and increase throughput.
- Quality Control: Implementing stringent quality control measures, including in-line inspection and statistical process control (SPC), to maintain high quality and reduce variability across large batches.
- Tooling and Fixturing: Designing specialized jigs and fixtures that can hold the parts securely and precisely during machining. This stage may also involve selecting or designing custom tools that can enhance machining efficiency and accuracy.
- Supply Chain Management: Establishing a reliable supply chain for raw materials and components to ensure a steady flow of inputs for uninterrupted production. This includes working with suppliers to maintain quality standards and manage lead times.
- Cost Management: Continuously evaluating and optimizing cost factors, such as material wastage, machine downtime, and labor costs, to achieve a cost-effective production process.
By carefully managing these aspects, manufacturers can efficiently transition from prototype to full-scale production, ensuring that the final parts not only meet the desired specifications but also perform reliably in their intended applications.
How to Get an Instant Quote for Your Custom CNC Machining Project
Online CNC Machining Services: Quick and Easy Quotes
In today’s fast-paced manufacturing environment, obtaining quick and easy quotes for your CNC machining projects is crucial. Online CNC machining services are designed to streamline this process by offering intuitive platforms where users can upload their CAD files, specify materials, and input additional project requirements. These platforms use advanced algorithms to generate instant quotes, providing you with a clear cost breakdown and lead time estimation within minutes. This not only saves time but also helps in efficient budget planning and timely decision-making.
Custom CNC Machining Services: Understanding the Cost Factors
Understanding the various cost factors involved in custom CNC machining services is essential for managing your budget effectively. Several elements contribute to the overall cost of a project:
- Material Selection: The type of material used can significantly impact the cost. Metals like aluminum or steel may be less expensive compared to specialized alloys or high-performance plastics.
- Complexity of Design: Intricate designs with tight tolerances require more precise machining and longer production times, which can increase costs.
- Volume: High-volume production often benefits from economies of scale, reducing the per-unit cost.
- Surface Finishing: Additional processes like anodizing, plating, or painting can add to the overall expense.
- Turnaround Time: Expedited services generally come at a premium due to the need for prioritization in the production schedule.
By understanding these cost factors, you can make more informed decisions and optimize your CNC machining projects for both performance and cost-efficiency.
Instant Quote: Streamlining Your CNC Machining Projects
The instant quote feature is a powerful tool for streamlining your CNC machining projects. By leveraging sophisticated software and cloud computing, these systems analyze your design files in real-time and offer immediate feedback on manufacturability and cost implications. This process eliminates the back-and-forth communication typically associated with traditional quoting methods, speeding up the entire project timeline. Instant quotes enable rapid prototyping, agility in design iterations, and a clear view of budgetary constraints, making it easier to plan and execute your manufacturing strategies effectively.
Maximizing CNC Machine Shop Capabilities for Custom Parts
5-Axis CNC: Advanced Machining for Complex Parts
5-axis CNC machining represents the pinnacle of flexibility and precision in the realm of custom part fabrication. Unlike traditional three-axis machines, which move linearly along the X, Y, and Z axes, 5-axis machines incorporate two additional rotational axes. This allows for the creation of intricate geometries and complex contours that would be challenging or impossible to achieve with 3-axis systems. Applications for 5-axis machining are extensive, spanning industries such as aerospace, medical device manufacturing, and intricate mold making. The ability to machine parts from multiple angles in a single setup reduces both production time and the risk of human error, leading to higher-quality, more precise parts.
CNC Lathe vs. CNC Mill: Selecting the Right Equipment for Your Custom Part
Choosing between a CNC lathe and a CNC mill depends largely on the specific requirements of your custom part. CNC lathes excel at producing symmetrical, cylindrical shapes by rotating the workpiece against a cutting tool. They are ideal for parts like shafts, bolts, and intricately detailed round components. Conversely, CNC mills are designed for removing material from a stationary workpiece through a variety of cutting tools. They are incredibly versatile and adept at creating complex parts with flat surfaces, slots, holes, and multi-sided features. Understanding the strengths and limitations of each machine type ensures you select the most efficient and cost-effective method for your custom fabrication needs.
The Role of Precision CNC in Achieving High-Quality Custom Machined Parts
Precision CNC machining is integral to producing high-quality custom machined parts that meet exact specifications and performance standards. Advanced CNC machines operate with exceptional accuracy, often achieving tolerances within microns. This level of precision is crucial in industries where even minor deviations can result in significant product failures, such as in aerospace, medical devices, and automotive sectors. Leveraging precision CNC technology not only enhances the quality and reliability of the finished parts but also optimizes production efficiency. High-precision machines reduce material waste, decrease production times, and minimize the need for secondary operations, ultimately leading to more cost-effective manufacturing solutions.
CNC Machining FAQs: Everything You Need to Know
Understanding the intricacies of custom CNC machining can be complex. Here, we address some of the most frequently asked questions to help you make informed decisions regarding your manufacturing projects:
What materials can be used in CNC machining?
CNC machining is incredibly versatile and capable of working with a wide range of materials, including metals like aluminum, stainless steel, and titanium, as well as plastics, composites, and even wood. The material choice depends on the specific requirements of the part, such as strength, flexibility, and heat resistance.
How does CNC machining ensure precision?
Precision is achieved through computer-controlled processes that follow detailed design specifications. Advanced software programs and real-time monitoring systems ensure that each cut, hole, or contour is executed with remarkable accuracy, often within tolerances of a few microns.
What are the limitations of CNC machining?
While CNC machining is exceptionally versatile, it has limitations, such as the complexity of internal geometries that cannot be reached by cutting tools and the feasibility of machining very small or delicate features that may require different manufacturing methods.
Custom CNC Machining: Solving Your Manufacturing Challenges
Custom CNC machining services are designed to address a wide array of manufacturing challenges. By employing state-of-the-art machinery and advanced software, custom CNC shops can tackle complex design requirements, meet tight tolerances, and produce parts with intricate geometries. This capability is essential for industries that demand precision and reliability, including aerospace, medical devices, and automotive sectors.
By utilizing custom CNC machining, manufacturers can also significantly reduce production lead times and material waste, which directly translates to cost savings. Additionally, custom CNC services offer flexibility in production volume, from prototyping to high-volume manufacturing, ensuring that all stages of the product lifecycle are efficiently managed.
Tips for Submitting a Successful CNC Machining Project
To achieve the best results from your CNC machining project, consider the following tips:
- Provide Detailed Specifications: Clearly outline all dimensions, tolerances, and material requirements. Providing a detailed CAD model can significantly improve the accuracy of the finished part.
- Select the Right Material: Ensure that the material chosen meets the part’s functional requirements. Consult with the CNC shop to determine the best material for your application.
- Optimize Design for Manufacturability: Simplify geometries where possible and minimize features that add complexity without necessary benefits. This can reduce machining time and costs.
- Communicate Clearly and Regularly: Maintain open communication with the CNC shop throughout the process. This ensures that any potential issues are identified and addressed promptly.
- Factor in Post-Machining Operations: Consider any additional processes such as heat treatment, surface finishing, or assembly, and communicate these needs early on to incorporate them into the project timeline.
By following these guidelines, you can ensure that your CNC machining project runs smoothly and achieves the desired outcomes.
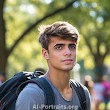