Printed circuit board assemblies (PCBAs) are the backbone of countless electronic devices. Ensuring their functionality and quality is crucial before they reach consumers. However, traditional PCBA testing methods can be time-consuming and prone to human error. This is where automation comes in, significantly accelerating the testing process while enhancing reliability.
Understanding the PCB Assembly Process
PCBA testing is the final step in a multi-stage process. Here’s a simplified overview:
1. Design and Engineering: The PCBA’s schematic and layout are created.
2. Procurement: Electronic components are sourced.
3. Assembly: Components are placed onto the bare PCB.
4. Soldering: Components are permanently fixed to the PCB assembly process using solder.
5. Cleaning: Any soldering residue is removed.
6. Testing: The assembled PCBA undergoes electrical and functional testing.
7. Inspection: The PCBA is visually inspected for defects.
Traditional PCBA Testing Methods
Before diving into automation, let’s explore traditional testing methods:
In-Circuit Testing (ICT): ICT verifies electrical continuity, opens, shorts, and component values. It requires physical test fixtures that can be time-consuming to develop.
Functional Testing: This method checks the PCBA’s functionality by simulating real-world operation scenarios. It can be complex to design and execute.
The Advantages of Automated PCBA Testing
Automation offers substantial benefits for PCBA testing:
Increased Speed: Automated testers can perform tests significantly faster than manual methods, reducing overall production time.
Enhanced Accuracy: Automation minimizes human error, leading to more consistent and reliable test results.
Improved Repeatability: Automated tests can be precisely replicated, ensuring consistent quality control.
Reduced Labor Costs: Automation can decrease the need for manual testing personnel, leading to cost savings.
Increased Data Collection: Automated systems can capture detailed test data for further analysis and process improvement.
Implementing Automated PCBA Testing Solutions
There are various levels of automation for PCBA testing:
Fixed Test Fixtures: These are custom-designed for specific PCBAs and offer a high degree of accuracy and repeatability.
Flying Probe Testers: These employ movable probes to test various PCBAs, offering flexibility for different designs.
Boundary-Scan Testing: This leverages built-in test features within components for efficient fault detection.
Choosing the Right Automation Solution
The ideal automation solution depends on several factors:
Production Volume: High-volume production often justifies the investment in fixed test fixtures.
PCBA Complexity: Complex PCBAs might benefit from flying probe testers’ flexibility.
Budget: The cost of automation solutions varies significantly.
The Future of Automated PCBA Testing
The future of automated PCBA testing is bright, with continuous advancements in technology. Here are some trends to watch:
Artificial Intelligence (AI): AI-powered systems can analyze test data to predict potential failures and improve test efficiency.
Machine Learning (ML): ML algorithms can learn from test data to optimize test parameters and identify defect patterns.
Cloud-Based Testing: Cloud-based platforms can offer remote access to testing resources and facilitate data sharing.
By embracing automation, manufacturers can significantly accelerate & how to test a PCBA, ensuring product quality and timely delivery.
Conclusion
In conclusion, automating PCBA testing offers a compelling solution to streamline production, enhance quality control, and reduce costs. As technology evolves, AI, ML, and cloud-based testing will further revolutionize this process. By adopting automation, manufacturers can gain a competitive edge in today’s dynamic electronics industry.
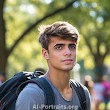