In the field of modern industrial design and manufacturing, choosing the right material is key to ensuring product performance, durability, and cost-effectiveness.
Polycarbonate and Acrylonitrile Butadiene Styrene are two widely used thermoplastics and often the materials of choice for many engineering projects.
These materials share similarities in various aspects, yet they also have significant differences, making the choice between them a challenge.
This article aims to provide a comprehensive perspective by thoroughly Polycarbonate vs ABS in terms of their chemical composition, physical properties, application areas, and environmental impacts.
It is designed to help decision-makers make informed choices based on specific needs and constraints.
Brief Description Of Polycarbonate And ABS
PC stands for Polycarbonate, a high-performance thermoplastic material known for its exceptional mechanical properties, transparency, and impact resistance, widely used in various industrial and consumer products.
ABS is a polymer plastic made from acrylonitrile, butadiene, and styrene, known for its excellent overall performance.
It combines strength, toughness, impact resistance, and surface hardness, and is easy to process and color, offering good dimensional stability.
Although ABS does not match the transparency of PC, it provides a more cost-effective choice in many applications.
Characteristic Differences
Here is a main performance comparison between these two materials:
Physical Properties
- Transparency: PC exhibits excellent transparency, making it suitable for applications requiring transparent materials, such as eyeglass lenses and bulletproof glass.
In contrast, ABS is opaque, suitable for products where transparency is not needed.
- Strength and Toughness: PC material has extremely high impact strength and maintains good toughness even at low temperatures, whereas ABS, while also possessing good toughness and impact resistance, is not as robust as PC in this respect.
- Heat Resistance: PC has higher heat resistance and can be used at higher temperatures without deforming, whereas ABS has lower heat resistance and is more likely to deform under high temperatures.
Chemical Properties
- Chemical Resistance: PC shows good resistance to many chemicals but is sensitive to certain solvents (like acetone).
ABS has good resistance to acids, alkalis, salts, and other types of chemicals but is sensitive to ultraviolet light.
- Water Resistance: Both PC and ABS demonstrate good water resistance, making them suitable for applications involving water contact.
Processability
- Processing Temperature: PC requires higher processing temperatures but can be processed by injection molding, extrusion, and thermoforming, among other methods.
ABS has lower processing temperatures, is easy to process, and is a preferred material for many rapid prototyping and injection molding applications.
- Paintability: ABS surfaces readily adhere to paint and other decorative coatings, whereas PC may require special treatment to enhance paint adhesion.
Cost-Effectiveness
- Raw Material Cost: Generally, the raw material cost for ABS is lower than that for PC, making ABS more popular in cost-sensitive applications.
- Processing Cost: Due to the ease of processing ABS, its processing costs are typically lower than those for PC.
Application And Samples
Polycarbonate is favored for many applications requiring transparent materials or those that must withstand extreme environmental conditions due to its exceptional transparency and high impact resistance.
For instance, PC is extensively used in manufacturing bulletproof glass and safety goggles, leveraging its ability to remain unshattered under high impact forces.
In the production of optical discs, such as CDs and DVDs, PC’s high transparency and good physical properties ensure accurate data reading.
Additionally, PC is very popular in the automotive industry for making transparent car parts like headlamp covers, as well as other components requiring high strength and heat resistance.
However, in the comparison of PP vs PET, PET far surpasses both PC and PP in transparency and exhibits higher recyclability, dominating the field of transparent packaging materials.
ABS is widely utilized in the electronics, automotive, and machinery industries due to its excellent comprehensive mechanical properties, good processing performance, and cost-effectiveness.
Electronic device cases benefit from ABS’s good dimensional stability and high surface quality, while its toughness and impact resistance protect the devices from damage during daily use.
The toy industry, especially for products like LEGO bricks, opts for ABS as the primary material because it not only provides sufficient strength and durability but is also easy to process into complex shapes.
Automotive interior parts, such as dashboards and door panels, are also commonly made from ABS, due to its exceptional aesthetics and wear resistance.
Environmental Impact Of PC And ABS
Despite the unique performance advantages that PC and ABS offer, making them indispensable in many applications, their environmental impact cannot be overlooked.
The production of PC requires significant energy and may release greenhouse gases and other pollutants during the synthesis process.
Although PC can be recycled, its recycling rate is relatively low, partly due to technical and economic barriers in the recycling process.
If untreated, PC waste, when landfilled, can persist in the environment for a long time due to its resistance to biodegradation.
In the production of ABS, chemicals such as acrylonitrile, styrene, and butadiene are used, which may pose risks to the environment and human health during manufacture.
Similar to PC, ABS can also be recycled, but the actual recycling rate is limited by the efficiency of collection and sorting, as well as recycling technology.
Improperly handled ABS waste can also have a long-term impact on the environment.
Conclusion
Polycarbonate and ABS are indispensable materials in industrial and consumer product design.
Their selection depends on specific application needs, including transparency, strength, heat resistance, and cost-effectiveness.
However, the environmental impact of these materials reminds us of the need to consider sustainability factors in their use.
Finding alternative materials, improving recycling technologies, and adopting more eco-friendly production methods are key ways to reduce the environmental impact of these plastics.
With advancements in material science and increasing emphasis on sustainable development, the future may see the emergence of more environmentally friendly and high-performance material options.
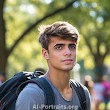